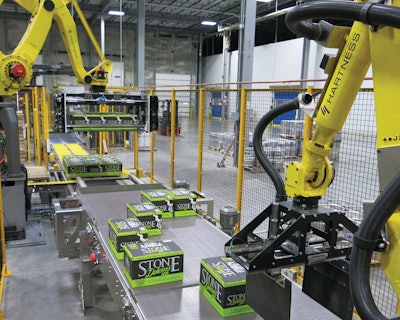
Since its 1996 debut, San Diego-based Stone Brewing built its reputation on remarkable variety and collaborations with other brewers, including special releases that are nationally distributed. The nearby Escondido, CA, bottling facility had grown over time to accommodate both short and long runs of a multitude of SKUs.
Given such roots, it would stand to reason that flexibility would be the primary motivating factor in choosing bottling and packaging equipment for a new facility. But while the beers retain their decidedly independent, craft character, the term “micro-brewery” no longer applies after more than 20 years of growth. In terms of volume, Stone now ranks in the top 10 of craft breweries in the U.S. As such, its latest bottling and kegging facility, opened in 2016 in Richmond, VA, represents a departure from its Escondido digs.
Most important, the new facility’s beer tanks are much larger than that of the California location, as they are tasked with accommodating the entire U.S. east of Colorado—and often handle overflow for the West Coast. Sited specifically to move upwards of 700 hundred thousand barrels a year in the future at peak production capacity, the equipment site-wide had to simultaneously match today and tomorrow’s volume while retaining flexibility.
Still, the seasonal and high-variety nature of the company had to be baked into the bottling lines as well, so as not to sacrifice flexibility for longer runs. According to Pat Tiernan, COO, the key was balancing the simultaneous needs for flexibility with large volumes to support growth in the future. Landed costs, alongside quality and cost of support, vaulted to the top of the Tiernan’s needs checklist.
“We plan to have the Richmond facility producing longer runs of fewer beer varieties, but to still have the flexibility to crank up some big collaborations and brews that are outside of our normal, core beers,” Tiernan says. “To do that, we wanted to be with vendors we could trust and we knew would be there when things happen, as they inevitably do at such a scale. We needed larger scale to support growth, but still do what Stone does from a creative and brand perspective, in the beers we produce.”
With two competing necessities on his hands, Tiernan aimed to keep it simple with all new, off-the-shelf equipment.
“For us, customization is undesirable,” he adds. “It’s better to go standard, in my opinion, if you can get it to work. That means ease of getting replacement parts, more service availability, and everything that goes with it. That will allow us to crank out that 700 thousand barrels of beer when the facility hits peak brewing capacity in the future.”
Flexibility versus throughput
A recent purchase at the existing Escondidio facility brings into stark relief the differing approaches at the two bottling plants. The West Coast facility received a major flexibility upgrade in 2016 with a Krones Varioline packaging line. Those configuring the Richmond facility, while doing so concurrently with the Escondido upgrade, chose not to go this route, highlighting the differing purposes of the two plants.
“Varioline is going to give you versatility and complex package setups for both secondary and tertiary packaging. This gives you versatility for unique configurations as demanded by the market. Sometimes the market wants a smaller package that fits in a refrigerator or cooler, and Varioline in Escondido allows us to make those changes on the fly,” says Mark Madonia, Stone’s Richmond Packaging Manager. “The Richmond facility is more for core product production runs and special releases.”
In fact, three varieties make up the lion’s share of the bottling at Richmond. The most commonly run bottle is four six-pack per case IPA, followed by a four six-pack of Delicious IPA or a 22-oz bottle Arrogant Bastard. Remaining runs tend to be of special collaborations or seasonal varieties, but these constitute considerably lower volume.
“So we don’t need the variation of packaging configurations that they might require in Escondido.Our packer is a unit that allows us to run certain packages with minimal conversion, and then we’re not hindered by conversion times,” Madonia adds. “The idea is changeover that’s simple and straightforward.” The packer he selected is a Hartness 2800.
Stone’s Richmond bottling line
A Hartness robotic depalletizer with an integrated DYNAC single-file bottle accumulator opens the bottling line. The standard 12-oz. empty amber bottles, supplied by a nearby Owens-Illinois facility in Toano, VA, travel overhead to an Arrowhead ArrowTower lowerator. After dropping to plant floor level, bottles are fed into a Hartness single-file accumulator and buffer conveyor prior to pressure-sensitive labeling using oriented polypropylene film labels.
“Using pressure-sensitive allows us to feature vibrant colors and unique tactile response cues on the label, yet remain extremely predictable in the manufacturing environment,” Tiernan says. “We tend to do a lot of branding on the bottle. For us, it’s a great way to let the beer on the shelf tell stories about the beer our fans enjoy.”
The labeler is a Krones Autocol 1235, which has requisite labeling checkmat inspection equipment and can operate at 660 bottles/min. Bottles are then conveyed into a 600 bottles/min Krones Modulfill HRS rinser/filler/ crowner block, complete with Moduljet rinser and fill-level checkmat. A Hartness DYNAC 7100 accumulator/conveyor exits the
rinser/filler/crowner, and a Krones Varioclean cleans the filled and capped bottles, which are then dried in a Sonic Smart Tunnel using air-knife technology. The Varioclean unit is sized to provide the clean in place (CIP) for the existing bottle line, but will also accommodate a canning line. In fact, most of the existing line, save for the rinser/filler/crowner, will be used for canning soon, as well as bottling, so most of the equipment will pull double duty.
Meanwhile, a Hartness case conveyor connects a Wayne Automation VCE high-speed case erector with a Wayne BCI 120 basket carrier erector and inserter. At the convergence of the case and bottle conveyors sits the aforementioned Hartness 2800 case packer. Finally, a Wayne UHS partition inserter and RPS glue case-top sealer closes the filled cases.
Both empty and full cases pass through Heuft case inspectors prior to reaching a Hartness robotic palletizer using Fanuc robots and Wulftec stretch wrapper.
Location, location, location
One site selection criterion that favored Richmond, VA, was a strong local talent base and similar nearby industries that could support such a large facility. Stone itself has honed and perfected a training program and certification process that they exported to the new site. Potential staffers have to clear a certain proficiency bar—all of them have to be able to maintain the equipment, for instance—and can potentially climb to higher levels and cross train against the line as they grow as employees.
“I like to joke around that before the Varioline, the old packaging line on the West Coast was like the opening credits on Laverne and Shirley,” says Tiernan. “We had old VW bug engines as compressors for our chilling equipment. But such equipment is easy to maintain, and when they did break, the skill level required to fix them is not as high as the new tech.”
But today’s electrician, tasked with maintaining such high-end robotics and equipment, has to be of a newer vintage. Richmond has a strong local talent pool of folks versed in PLCs, ladder logic, and code writing, making it attractive.
“On the West coast, we struggled with this a little as the technology had greatly changed, so we’ve had to ramp up our training programs and the skill levels of the people on the team,” he says. “We benefitted by not having to do that in Richmond, because we could seek out the
right skillsets.”
And this brewery has a history of being a good neighbor and steward of the locations it calls home. In this case, while the brownfield site moved from blueprint to reality, Stone worked with the City of Richmond to develop training programs preparing technically proficient potential employees for the specifics of brewing and bottling.
“Another thing that really attracted us was the level of outreach, from brewers, from community members and economic development folks, from various levels of government, and from local universities,” Tiernan says. “There are three universities in town, and we participate in various forms with all three of them. And they’re interested in us, putting together specific programs for craft brewing or other operational and packaging elements. The technical proficiency is here, but specific to brewing and brewery plant operations, the East Coast maybe needing to catch up a bit to the West Coast. We can team with these universities to make that happen.”
Fully automated and integrated
As on most Krones equipment, control level software uses Botec HMI interface, and Siemens controls and PLCs. The company interfaces the shop floor system with Ignition MES software by Inductive Automation. Ignition handshakes with the Microsoft Dynamics AX ERP system, so from material in to beer out, it’s all scan in, scan out, and fully automated online.
“It’s a pretty dialed-in operation,” Tiernan says. “Ignition is a highly flexible, programmable platform that allows us to do everything from data management and business intelligence to shop floor controls.”
Even in a simple and low-support/low-overhead version of the software—and without having to pay a bunch of consultants—Ignition software allowed Stone to create its own shop floor systems and integrate them freely.
“Plus, it doesn’t lock you in to the more robust versions of the system in the future,” he says. “It was a great way to connect a new ERP system with some of the existing controls and shop floor work that had already been done in Ignition, and tie it all together.”
Equipped with this MES software, and its own set of KPIs and dashboards, Stone’s next step is to link the Escondido facility, the Richmond facility, and even a Berlin, Germany brewery and bottling plant that was developed in parallel with Richmond. When connected, all operators can see what’s running, and where, at any time. It’s thought that Richmond will handle some West Coast production overflow, making connectivity important. More practically, they can compare planned outcome with actual results, can observe all quality-control parameters, can run charts to improve production or identify problems, and have access to all the main dashboards all through one system.
“We have two engineers who spend part of their time developing and maintaining that system, so as we add more capability on the floor, it’s very easy to plug in a new PLC or to reset a schema in one part of the operation versus the other, or program in, for example, sequencers on our centrifuge and filtering operation,” Tiernan says. “It’s just very well adapted for our purposes, and it’s flexible enough to run all of our breweries.”