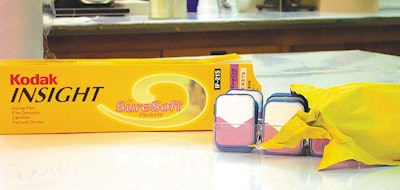
Among the many film products made by Eastman Kodak Co. are dental film “packets” used for tooth x-rays. These consist basically of x-ray film and other key components sandwiched between two pieces of vinyl. Once these layers are joined together in large sheets, individual packets are die-cut, packed, and shipped.
Because the die-cut edges can cause discomfort in the patient’s mouth, product development specialists at Rochester, NY-based Kodak designed a softer, gentler packet, one with a soft vinyl cushion added to the perimeter of the packet after the die-cutting process. Launched this past summer, the new product is called SureSoft packets.
Working closely with the product developers was Michael Marou of Kodak’s Package Engineering & Graphic Design group. It quickly became clear, says Marou, that “Our standard approach to packaging wasn’t going to work with the SureSoft packet line.”
The “standard approach” to which Marou refers consists of bundling 150 packets in a polyester band and then flow wrapping them in a film/foil lamination before sending them through a cartoner. This approach was discarded for the SureSoft packet line to prevent any damage to the soft edges of these new packets by the PET band.
What Marou and colleagues came up with as an alternative is a PET tray in place of the PET band. Thermoformed of recycled PET by Placon (Madison, WI), the tray has eight compartments that are filled by hand, 10 packets per cavity. Trays then proceed through a flow wrapper from Fuji Formost (Woodinville, WA) and a cartoner from Bivans (Los Angeles, CA), both of which have been in use at Kodak for some time.