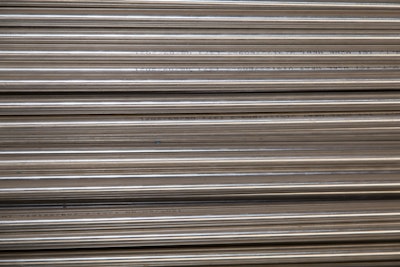
This content was written and submitted by the supplier. It has only been modified to comply with this publication’s space and style.
As with other aspects of heat exchanger design, the choice of construction material depends on a number of factors based on the end use. There are a number of advantages to the use of stainless steel over carbon steel, which is why HRS Heat Exchangers use 316L stainless steel for the corrugated tubes in its heat exchangers and 304L stainless steel for the outer shell.
As well as the hygiene benefits in food and beverage applications, there are also advantages in terms of performance. 316L stainless steel is an austenitic stainless-steel alloy with low carbon content, making it resistant to corrosion and ideal for use with dairy products.
This corrosion resistance means the heat exchanger walls can be thinner, and because of the improved heat transfer, using corrugated stainless-steel tubes results in a smaller overall footprint for the heat exchanger.
The final exchanger may also include fewer, or smaller, modules to deliver the same or better performance compared to an equivalent model using straight carbon steel tubes. The smaller footprint and lighter construction also mean that ancillary and associated civil engineering costs are also lower.