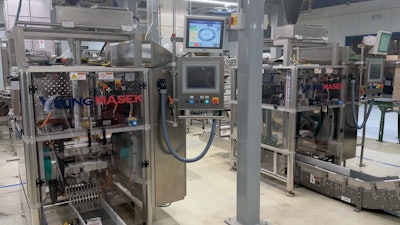
Darlington Snacks is a thriving family-owned snack manufacturing and packaging facility located in the vibrant city of Joplin, Mo. Established in 1982, the company has grown from a small local operation to a respected national player in the snack industry. Darlington Snacks prides itself on producing high-quality, innovative, and delicious snack products that cater to a diverse range of consumer tastes.
Serving daycares, schools, and the healthcare industry, Darlington Snacks is committed to sourcing the finest ingredients for their products. They partner with local farmers and suppliers whenever possible, supporting the local economy while ensuring that the freshest and highest-quality ingredients go into their snacks. This dedication to quality has earned the company a reputation for producing some of the tastiest and healthiest snacks in the nation.
Not long ago, management at the snack food company recognized that they faced significant challenges where staffing was concerned. Located as they are in an area dense with food manufacturing plants, they faced tough competition when it came to finding talented workers. With many open manufacturing jobs, they were scrambling to fill positions and overstressing current employees when trying to keep up with demand.
Also challenging was delivering packaging accuracy and being able to meet customers’ product handling requests. Being in the foodservice business for schools and healthcare institutions, the firm faced increased demand for snacks in single-serve containers that weren’t going to be handled by multiple parties, especially during the COVID pandemic.Above the baggers are two combination scales fed by vibratory conveyors.
At PACK EXPO Las Vegas 2021, representatives from Darlington Snacks saw the impressive speed of the Viking Masek Velocity vertical form/fill/seal packaging machine filling single-serve pouches. Brad Schweiss, vice president of manufacturing at Darlington Snacks, was already familiar with Viking Masek’s packaging equipment.
“I’d been with Darlington for six years but in the industry for more than 30,” explains Schweiss. “So I was familiar with Viking Masek and what their services and capabilities were.”
After collaborating with Viking Masek’s team of snack packaging experts, Darlington Snacks purchased an entire snack packaging system consisting of two bagging lines that merge into a single case packing line. On each bagging line, the process looks like this.
Vibratory infeed
Snack products first make their entrance into the automated packaging system through a vibratory infeed hopper from Eriez and then are fed to a Whiz Lifter Model C bucket elevator from Frazier & Son. It conveys the snacks vertically to an Eriez feeder that delivers the product to an ADW-0-0120F 20-bucket combination scale from Yamato where it is quickly and precisely weighed. Next the snacks are gently dropped into bags that have been formed on the vf/f/s Velocity packaging machine at a rate of 150 bags/minute on each machine (300 bags/min for both bagging lines).Closing jaws on the vertical form/fill/seal.
Featuring controls from Rockwell and patented servo-driven dual-jaw technology, Viking Masek calls the Velocity the “Fastest VFFS Packaging Machine in the World.” It’s capable of production speeds to 300 bags/min. The unique center-mounted filling tube and naturally counterbalanced sealing profile are designed to provide vibration-free, extremely smooth operation at all speeds. The machine is also versatile, producing packages as small as 60 x 90 mm (0.66 x 3.54 in.) or as large as 300 x 1000 mm (11.8 x 39.37 in.). Its versatility was appealing in Darlington’s case as the firm produces bag sizes ranging from 4.25 x 5.5 in. to 8 x 10 in.
Integrated into the Velocity bagger is a continuous ink-jet coder from Linx that marks each bag with date code information. The bags are sealed shut and drop onto a Z-shaped takeaway conveyor supplied by Multi-Conveyor. The finished bags pass over a Yamato CSJ22L-00/CE31 checkweigher to ensure accuracy before dropping from the Z-shaped Multi-Conveyor and through the basket of a batch gate from AS&E right into a waiting case below the gate. Inside the basket is a light curtain, so each time a bag drops through that curtain it gets counted. When the correct number of bags has been counted, a signal is sent to the controller of the Velocity bagger and that controller sends a signal to the batch gate to close long enough for the filled case to be conveyed away and for a fresh case to be conveyed in. With the fresh case in place, the batch gate opens and bags continue dropping into the basket for the next batch.
One minor feature worth mentioning is that when a case is being filled, a pair of vacuum cups attached to pneumatic devices attach themselves to the bottom sidewall of one side of the case and stroke constantly in and out. This bit of agitation ensures that the pouches are spread evenly across the case rather than grouping all in one part of the case.Corrugated cases are erected on this system and sent on a roller conveyor that brings them to one of two right angle conveyor spurs, each leading to a batch gate that counts bags into cases.
As for case erection, it takes place not far from where the two AS&E batch gates are located. A Veritiv Lantech C-400 erects corrugated cases from flat blanks. It puts them on a roller conveyor that leads to two right angle conveyor spurs. Each of these spurs leads to an AS&E batch gate, and cases move into these gates based on demand. Once a case has received its batch of bags from a batch gate, it’s carried away at another right angle on a roller conveyor that takes cases in a single file to a Veritiv Lantech CS-300 case taper. A short distance later the cases pass through a Foxjet ProSeries Trident ink-jet printhead controlled by a Foxjet Marksman Matrix controller. As finished cases reach the end of the line, they are stacked manually onto pallets, and the pallets are then moved to a storage area where they await their journey to schools, daycares, and health care facilities across the country.
This entire snack packaging line was set up, tested, and perfected at Viking Masek’s US headquarters in Oostburg, Wis., before it was even loaded on a delivery truck.
Trial run
"Before delivery of our automation, I took my plant engineer to Viking Masek to see the system’s capabilities, slow-motion videos for assessment, and a trial run of the line before it shipped with everything labeled the way we needed it to be,” explains Schweiss, who adds that he was quite impressed with Viking Masek’s comprehensive testing and checkout process.
Viking Masek assembled the entire system onsite at Darlington Snack’s plant. The new snack packaging lines fit seamlessly into their packaging configuration, resulting in precisely the solution their customers were asking for.
“We didn’t have to worry about integration because Viking already took care of that for us,” comments Schweiss. “We bought it as a complete system and it’s functioned perfectly since.” Darlington Snack’s biggest victory with the automated packaging system is the accuracy of the batch gate–they report it’s consistently spot on.
“The real trick for me was the downstream stuff to be able to make the counters work right,” explains Schweiss of the accuracy of their packaging line. “We had to be able to get the cases erected and into the two stations in the right sequences at the right time, and then on out to the palletizing operation. It has worked seamlessly.” Today, Darlington’s packing operation, case conveyance, and case closing are all automated. Staff members who formerly were required to conduct such operations have been relocated to other areas of the facility. Since embracing automation, Darlington Snacks has seen substantial improvements with the throughput and labor-related challenges they were facing.
“Automation has cut down on our waste, overpacking, and amount of giveaway,” reports Schweiss. “It has made our customers’ experience better because we’re not coming up short on products. And I’m pleased to report we’ve doubled production with about 40 percent less labor on the line.”Shown here is one of the two conveyor infeeds leading to the batch gate counter.
As a single-source provider, Viking Masek takes care of everything, from sourcing the packaging line components, to assembly and testing, to delivery and setup, and finally technical support of the entire system.
“Viking Masek helped us tremendously as a single-source provider for the entire line. Our post-sale support has been beneficial and responsive. When we have an issue, Viking Masek takes care of it,” comments Schweiss. “I’d definitely recommend Viking Masek to anyone looking at automating their packaging operation. The fact that I’ve worked with Viking Masek in the past and wanted to work with them again demonstrates how much I value their expertise.” PW