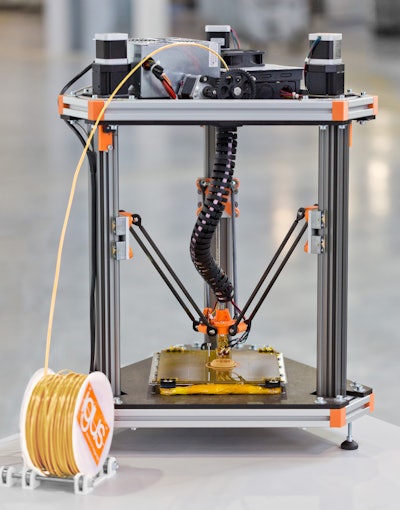
Igus has introduced a plastic filament for 3D printers enhanced with tribological or low friction properties. The material is resistant to wear and abrasion and is ideally suited for creating custom bearings.
The company has been researching filaments for 3D printers to provide customers with more flexibility in their design ideas. Now, customers can design custom parts or manufacture prototypes while still relying on the service life of igus plastic materials.
This product is the first filament for 3D printers specifically developed for motion control applications. Currently, igus offers 45 high-performance plastics as optional materials for iglide products, with a further 100 custom materials suited to specific, demanding customer needs. Moving forward, the new filament will give customers more flexibility for the design of their application’s bearings. Even prototypes can be produced quickly and cost-effectively, according to the vendor. Igus also offers access to 3D models of its products in STL format, which can be easily downloaded and used directly as input data for 3D printing.
3D printers are able to print full-size, three-dimensional objects. This up-and-coming technology will reduce the high tooling costs of part production and eliminate waste as only the desired object is printed. With the proper computer software, any printed component can be customized to the exact shape and size desired making otherwise impossible-to-find parts available and affordable.