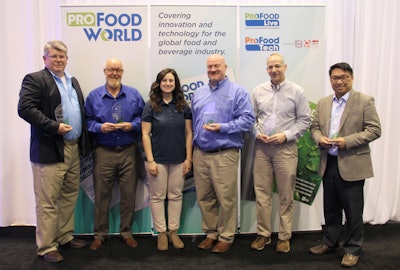
The winners of ProFood World’s 2018 Sustainability Excellence in Manufacturing Award prove that eco-friendly activities and profitability go hand in hand. ProFood World honored the award winners in Chicago during ProFood Tech, where they shared how their operations go beyond environmental compliance and drive improved performance through sustainability.
First Place Program Category
In the Program Category, Smithfield Packaged Meats’ facility in Kinston, North Carolina, earned first place for making some simple, cost-effective adjustments to its smoker to prevent excessive liquid smoke loss. Prior to initiating the project, the company lost about 1.62 gal per hour of liquid smoke when it applied the liquid smoke to its hotdogs. The liquid smoke dripped off the hotdogs and seeped into the floor drain, causing Smithfield to lose about 38.88 gallons of liquid smoke per day at a cost of about $22.57 per gal. In addition, it increased the company’s surcharges for wastewater treatment. Smithfield decided to install a blower and air knives that it wasn’t using on one of its dryers onto its smoker unit. The blower system with air knives blows the excess liquid smoke off the baskets holding the hotdogs into a smoker holding tank. By making this simple change to its smoker, Smithfield reduced its liquid smoke loss by 59 percent and saved more about $129,000 in a year by capturing the excess liquid smoke. Because the company already had the blower and air knives on hand and only needed to purchase about $300 of parts for the installation, the return on investment was immediate.
Second Place Program Category
Land O’Lakes’ facility in Kent, Ohio, received the second place award in the Program Category for converting butter into energy. In 2016, the Kent facility spent $41,000 in environmental cleanup for its 10-ton trash compactor, which leaked butter, and removing it three times a week. The company decided to find a better way to discard its packaged butter products that it couldn’t sell for various reasons, including line casualties, lab samples and out-of-spec products. Instead of putting the products in its trash compactor, Land O’Lakes now works with a company that has an industrial shredder with a high-pressure, high-temperature press on the back side of it. As the shredder heats up, it presses the melted butter, which goes through a screening device and to an anaerobic digester. Micro-organisms in the anaerobic digester consume the butter, producing electricity, heat and methane gas. The plastic from the products are recycled. Land O’Lakes no longer has environmental cleanup fees, saving $41,000 a year. It only removes the compactor waste once a week, compared to three times a week in 2016—reducing pickup charges by two-thirds. The company diverts 282 tons of butter from the landfill to the anaerobic digesters, generating 149,000 kWh of electricity in 2018, which is equivalent to 1.5 percent of the total kWh that the Kent facility uses every year.