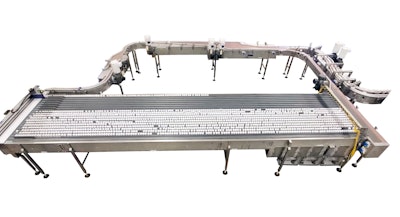
This content was written and submitted by the supplier. It has only been modified to comply with this publication’s space and style.
Pack Air Inc.’s latest achievement is building a custom-made Multi-Lane Accumulator for food or non-food products. This Multi-Lane Accumulation conveyor system can store 1.25” to 1.75” diameter cylindrical-shaped products at a rate of 350 products per minute, and hold approximately 3000 products for more than 8 minutes of total accumulation. Here’s how it operates.
Products are diverted off the main line with a simple pneumatic paddle and directed towards the accumulation table. At the infeed of the table, the product contacts a small powered 90 degree curve conveyor that is mounted to a linear guide. The powered turn helps guide the products into the first lane of the table and that lane is filled at a rate that maximizes capacity but also minimizes product contact and pressure.
Once the photo eye senses that the product is at the end of the first lane, the powered curve transfer moves on the linear guide so the product can start filling the second accumulation lane. Photo eyes on the powered curve help guide the transfer to maximize the fill rate of each lane. This process continues until all the lanes have been filled up or the production line is ready to reintroduce the accumulated product.
Products follow a true FIFO product flow by systematically filling and emptying individual lanes of product. Once the signal has been made to release the accumulated product, the first lane releases everything back into the production line. The second lane starts to release the product back into the production line once the photo eyes sense that the first lane is empty. This process keeps reintroducing the product in a FIFO order until the accumulation table is completely clear of the product.
If the product needs to be accumulated again before the table empties, the powered curve transfer resets itself back into the first lane to accumulate the product. The first lane product will only be reintroduced into the production line when all previously filled lanes have been emptied.