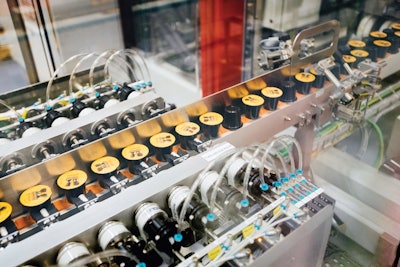
Westrock Coffee Co., North Little Rock, AR, is a premium-quality coffee products manufacturer, advocating sustainable growth at the point of coffee origin and transparency throughout the supply chain. The company markets coffee products in conventional bagged (whole beans and ground) packaging. But recently they decided they wanted to tap into the growing market for single-serve dry ground coffee pods, the kind that go into coffee makers popularized by the likes of Keurig. Chief Marketing Officer Elizabeth McLaughlin describes the new venture this way.
“We want to partner with all types of customers to meet their coffee program needs. We work with foodservice partners, hotels, and others in the hospitality industry who need a co-packer for this coffee format, as well as with retailers who sell branded and private label, single-serve coffee.”
In August, 2014, after investigating various options, Westrock opted to install an entirely new and highly automated packaging line, including a Rychiger AG filler/sealer for pre-made polypropylene single-serve coffee pods and a Model 424 wraparound cartoner from Somic America, Inc. The Somic system collates the filled/sealed pods into 12-, 18-, or 24-count cartons and then wraps a paperboard carton around them. The high-end, high-efficiency line, designed and specified largely by Rychiger, has served to keep labor costs in check while delivering high-quality single-serve packs.
“We think the Rychiger AG FS910 filling machine is the most advanced option on the market to fulfill our desire to produce high-quality, single-serve pods at high volumes and speeds,” says McLaughlin “It was Rychiger’s recommendation that we utilize the Somic cartoner as the most efficient and effective means of multiple-format cartoning of these single-serve packs.
“Rychiger AG and Somic personnel were invaluable to the success of the line. Technicians from both companies provided installation, set-up, training, and production support for the launch of the line in August 2014, and their support remains crucial as we grow this market segment.”
Getting it together
Filling on the Rychiger machine is done 10-across at an impressive 550 to 600 pods/min. Nested stacks of empty pods are placed in 10 vertical magazines, and from these magazines the pods are picked and placed into pockets on the carrier plates that take them through the Rychiger machine.
Printpack supplies the pods, each of which holds 10 g of coffee. Printpack first coextrudes the PP/EVOH/PP sheet and then thermoforms the pods. The use of a proprietary PP blend, says Printpack, ensures that each pod will puncture smoothly in the consumer’s single-serve coffee brewing machine. Printpack also indicates that, because its pod substitutes PP for the polystyrene that is used so commonly today, the opportunity for recycling of the pods is greater, moisture resistance is better, and, because PP is less dense than PS, less material is required in the making of a pod.
The other key packaging component in the pod is the lid. Supplied pre-cut and flexo-printed by LMI Packaging Solutions, it consists of aluminum foil and a heat seal coating. The pod and lid structure combine to provide a 12-month shelf life.
Returning to the Rychiger system, it consists of a series of modules, each of which uses specialized tooling to perform some portion of the overall packaging process. At each module, pods are lifted into the tooling and then dropped back down into the carrier plates for transfer to the next module.
A short distance from the pod denesting station at the very beginning of the Rychiger, the pods enter a filter forming module where small discs of filter paper are cut and formed into the bottom of each pod. Pods then advance into an ultrasonic welding module that welds the filter to the pod. Why the filter paper? Because during brewing, a needle punctures the top of the pod and the bottom of the pod. From the top, hot water is injected into the pod under pressure. Freshly brewed coffee comes out the hole that is punctured in the bottom. The role of the filter paper is to prevent grounds from getting into one’s coffee cup.
Next up is the dosing module, where servo-driven augers deposit precise amounts of coffee into each pod. Tooless changeover of augers, funnels, and nozzles is a distinguishing characteristic of the Rychiger system. So is its accuracy. Right after dosing is complete, each pod is lifted into a load cell to be weighed, and the weight is communicated to the central controller. If the amount of coffee in a pod is drifting off target, the auger can be adjusted on the fly. “We’re consistently within one-hundredths of a gram of where we want to be,” says Chief of Single Serve Operations Brett Burton.
Lidding
At this point it’s nearly time to apply the pre-cut lids, but only after the pods pass through a rim-cleaning module that uses vacuum to clean the rim of each pod to eliminate any chance that coffee or some other foreign object might compromise a tight seal.
In the lidding module, nitrogen is flushed across the head space just before heat sealing takes place. Then a high-speed vision system ensures that each pod has a properly seated lid. If anything is outside of predetermined parameters, that pod is rejected.
The final module of the Rychiger system is a pick-and-place tool that takes 10 pods out of their transfer plates and puts them single file on a conveyor that leads to a large accumulation/transfer conveyor from Arrowhead that leads to two discharge gates. This conveyor is equipped with three belts, and the one farthest to the right runs south to north. So does the one beside it, but at a quicker pace so it moves the pods out of a mass flow and into a narrower stream of pods. The belt farthest to the left runs in the opposite direction of the other two. So pods that don’t enter the two discharge gates of the Arrowhead accumulation/transfer conveyor are gently re-circulated back into flow. “Arrowhead makes these kinds of systems for all kinds of applications,” says Burton. “This one was custom built to Rychiger’s specs for our particular requirements.”
Mentioned above were the two discharge gates of the Arrowhead accumulation/transfer conveyor. One of these takes pods through a U-turn and then into a bulk packing station. “Essentially it’s a pair of feed screws that can be programmed to drop as many pods as we like into whatever size corrugated shipper or tote we want,” says Burton. “Might be 80 pods, might be 500. Once the sensors detect that the desired number of pods have dropped, the screws stop while an operator puts another container beneath them.” When it’s a corrugated case being filled, the operator puts it on a conveyor leading to a Little David top taper from Loveshaw. Also used is a Little David thermal-transfer print-and-apply labeler that puts date and lot codes on the bulk containers.
The other discharge gate out of the Arrowhead accumulation/transfer conveyor leads to the Somic 424 wraparound cartoner. Upon entering this machine, a pair of star wheels meters the pods onto the vacuum belt that brings the pods two across into the wraparound cartoner.
“We don’t like a lot of mechanical guiding when it comes to infeeding the containers,” says Peter Fox of Somic. “No side guides or top guides or that sort of thing. We prefer to control the position of the container by vacuum, which we find very effective. The pod in this case has a slightly recessed bottom that improves our ability to form a secure vacuum and keep each pod where we want it on that infeed conveyor.”
Product manipulation
Next up is what Somic calls “product manipulation,” which arranges pods to a predetermined orientation, either upright or inverted. This allows them to nest more compactly, thus keeping carton costs to a minimum. How many it inverts and which ones it inverts can vary. “It depends on the pack pattern,” says Fox. “It’s intelligent in that it knows what stage it’s at in the process of container orientation.”
The product manipulation tooling is fascinating to watch. Essentially it’s a reciprocating carriage with eight pairs of vacuum flippers adapted to the pod shape. When the carriage strokes back to begin a cycle, paired flippers that need to invert pods close in on their assigned pod from opposite sides. Using vacuum grippers, they lift the pod from the vacuum belt, invert it, and release it back onto the vacuum belt. Then the carriage strokes back to repeat the cycle. “There are 26 servo motors on this cartoner,” says Fox. Also crucial, he adds, is the decentralized PacDrive control system from Schneider Electric. “Not only does this optimize what is a complex array of servos, but it also significantly reduces the control cabinet size, further contributing to a small footprint.”
Next the pods are conveyed into the pick station, where pick-and-place tooling uses vacuum cups to pick 24 pods and place them into four collator bins, six pods per bin. The pick-and-place tooling then places another 24 pods atop the first layer. So at this point each bin has 12 pods compactly arranged in two layers. The bins are mounted on an oval-shaped racetrack sometimes referred to as the “lamella chain grouping system.” Once each of the four bins has its full complement of 12 pods, the servo-driven bins advance to a station where two servo-driven arms push the pods from their bins onto a flat carton blank. When the 12 pods arrive on the carton blank, they’re in a square metal forming cassette, so the carton blank is formed around this cassette rather than around the unsupported stack of pods. This helps ensure a perfectly squared-up carton every single cycle without putting the kind of pressure on the pods themselves that could result in damage.
Following a brief dwell time during which the adhesive on the wraparound carton has a chance to set up, the forming cassette retracts and the carton moves into the next station. Here the top cover has hot melt adhesive applied and is pushed into the closing station while folding down the glue flaps. The carton is closed when the reciprocating head folds the cover and seals it to the three inside flaps. The closing head lifts and releases the finished carton for discharge.
Manufactured to Somic’s specifications, the 100% recycled paperboard carton flats are supplied by Frankston Packaging and feature artwork printed in a four-color process. For the Westrock cartoning application, the two-lane dual-load Somic 424 system is engineered to run at up to 600 capsules per minute.
Also worth pointing out is that like the pod infeed and handling stations upstream, the cartons are also controlled and moved through the cartoner on vacuum conveyors.
Cartoning satisfaction
Westrock worked closely with the equipment systems suppliers to install and start up the new coffee pod packaging system, and they found that the Somic America and Rychiger machinery were highly compatible and relatively easy to integrate. Westrock also has found this system to be much more efficient than using a traditional pick-and-place operation to load the pods into preformed cartons. It also saves considerably on floor space because the Somic 424 takes the place of a more traditional carton erector/loader/closer line configuration.
McLauglin notes, “Our Somic 424 provides us the ability to package cartons in numerous formats, with current offerings being 12-, 18-, and 24- counts of coffee pods. The tool-less components of the Somic cartoner make changeovers to different formats fast and easy. An average changeover operation can be accomplished by two people in as little as 20 minutes, allowing us flexibility for possible future pack format diversification. Our current 12-count formats are produced at rates up to 53 cartons per minute, and the 18- and 24-counts are produced at rates of 34 and 26 cartons per minute, respectively. For master shipper casing of these cartons, we use case packing equipment from Focke & Co.”