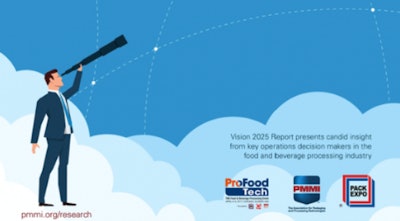
Earlier this year at ProFood Tech 2017, PMMI conducted focus groups with food and beverage professionals who have primary responsibilities in processing operations. Part two in this series of articles focuses on how innovation can bring order to chaos for food and beverage manufacturers.
According to PMMI’s 2017 Vision 2025 report, CPGs are using more focus groups to collect “voice of the consumer” feedback to avoid failed product launches. Internally, CPG companies are improving cross-functional collaboration with the use of OpX Leadership Network programs such Factory Acceptance Testing programs, employing more upfront project planning, and working more closely with marketing colleagues to get a better understanding of how to meet customer demands.
Concerning equipment, more CPGs are leaning on suppliers for help with process improvements, and prototyping and proof of concept pilots. Most manufacturers want to build a true partnership with suppliers, but some CPG are implementing supplier performance agreements with clauses that require compensation if performance is not met. This forces candid conversations regarding realistic expectations. Manufacturers are also demanding corporate social responsibility from suppliers and are including it in supplier agreements.