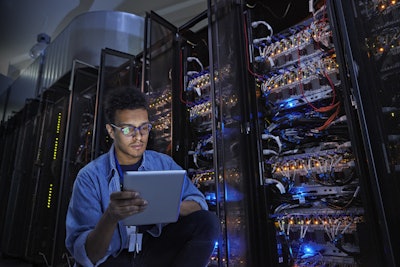
Vision 2025 Tackles the Future of Workforce Preparedness
Some of the major challenges include:
- Community colleges and technical schools need to provide adequate training for a more versatile maintenance and operations skill set.
- The best ways to foster workforce engagement to improve uptime reliability.
- Balancing the increasing use of robotics to offset labor shortages.
- Lack of availability of skilled talent at all levels, especially where automation is involved.
- Resistance to change among workforce.
- Uncertainty regarding skill requirements for the future.
- Dedicating training time – taking people off the production floor to train.
- Finding, and affording, high-quality labor.
Solutions being considered or implemented:
- Substantially upgrading technical training.
- Connecting with teachers/professors in local community colleges to make them aware of our needs and help us connect with their students.
- Actively participating in and sponsoring First Robotics program and other events involving students to recruit them as interns.
- Inviting students to let them see what a career in manufacturing could be like for them.
- Partnering with charter schools and other educational institutions to feed internship programs.
- Looking at the traditional European model of apprenticeships as a model.
- Expanding mentorship program.
- Making training videos in-house (YouTube) where seasoned veterans demonstrate proper techniques, procedures, etc. in production operations.
- Documenting the ROI of technical training more effectively to show that it clearly works.
- Using OEM produced videos to help operators with training and troubleshooting of equipment.
Learn more about key manufacturing challenges that were discussed during Vision 2025, and download the entire 20-page report for FREE here.
Learn more about PACK EXPO Las Vegas 2019 here.