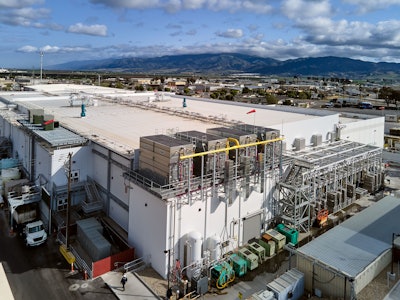
In April 2022, Taylor Farms’ flagship facility in Salinas, Calif., suffered a devastating fire where their main foodservice leafy green production facility was located. The fire started between the walls of the decades-old structure, and the blaze eventually made its way to the roof, collapsing it in flames and destroying the 60,000-sq-ft of processing space. The larger building structure surrounding that production area remained mostly intact.
In the immediate aftermath, the company decided to rebuild the facility on the same real estate . CEO Bruce Taylor also set the bar high with a one-year deadline to finish that project. Meanwhile, customer deliveries of triple-washed lettuce, romaine, cabbage, baby spinach, baby spring mix, and green leaf would go on as scheduled, leveraging the company’s network of plants and distribution to pick up the slack, relying on a seasonal facility in Yuma, Ariz., and other local facilities near Salinas, California for processing and shipping.
Right on schedule, Taylor Farms reopened in April 2023, but along the way the company and design/build partner Dennis Group encountered obstacles of every kind, from supply chain issues for materials and components to catastrophic weather events like an atmospheric river that turned the construction site into a mud pit, and flooded Salinas as well.
After Taylor Farms' processing facility in Salinas, Calif., burned down, the company set an ambitious goal of one year for a complete rebuild.Dennis Group
“This factory was our first factory in California. This was our first home for Taylor Farms, and it was like family coming together after losing their first house,” says John Krbechek, VP of engineering at Taylor Farms Foodservice Division. “Failure [to rebuild] was not an option.”
Today, Taylor Farms has a state-of-the-art processing plant with a weekly production volume of 15 million lb of fresh-cut produce. It’s one of the highest capacity plants of its kind in the industry, and because of this phoenix-like rise from the ashes, Taylor Farms has earned a Manufacturing Innovation Award from ProFood World. Here, we’ll detail how Taylor Farms used the blank slate of reconstruction as an opportunity to increase efficiencies in processing, sustainability, sanitation, and much more.
Rerouting production
The strategic triage enacted after the fire by Taylor Farms began with making sure customers received their produce orders without interruption, while detailed plans
Taylor Farms has 22 production locations across North America, and depending on the location, produces a combination of fresh vegetables and fresh food items for restaurants, schools, grocery stores and convenience stores. The Salinas plant that burned down was dedicated to the foodservice market segment, so production remained in the seasonal sister facility for an extended term in Yuma, while a logistical system to service customers was created to receive raw produce and finished produce from six other coolers.
Every year between April and November, leafy greens are grown and processed in Salinas. Then from November to April, production equipment is trucked from Salinas to Yuma to continue processing, since that’s when leafy greens are grown and harvested in that region.
![]() | See how Riverbend Ranch's beef processing innovations earned it a 2024 MIA nomination. |
Serendipitously, because the Salinas fire happened in April, all the equipment necessary to continue processing greens in Yuma was still there, about to be sent back to Salinas. So, Taylor Farms kept operations going in Yuma, sending raw vegetables now being harvested in Salinas to Yuma for processing, then back to Salinas to be shipped to clients.
With those immediate production problems solved, Krbechek and Jeffrey Lewandoski, senior partner at Dennis Group, turned their attention to rebuilding the Salinas plant and using the opportunity to upgrade and modernize the facility from the ground up.
Here you can watch a timelapse video of the interior of the plant being built and populated with processing equipment.
“It was pretty devastating when we were looking [into the ruins] and it was still smoldering. We had big evaporative coils that were just melted into a pool of aluminum,” says Krbechek. “The surrounding building structure survived the fire but the infrastructure, electrical, refrigeration, water, and all the utilities had to be redone, rerouted, or reconfigured.”
Sanitation Strategies
Starting from scratch meant Taylor Farms could build a new plant envelope up to the very latest hygienic standards, and those high standards would apply to everything inside that envelope. “The whole facility is a food-safe, sanitary washdown space, including walls, ceilings, floors, and drains—there are no points that can’t be cleaned,” says Lewandoski. “Nothing is tight to the walls that you can’t clean behind. We have two-inch standoffs on all piping, conduit, racks, and everything is washdown ready, from the lights to the doors to the frames, everything can get wet, soaked, and sanitized,” he says, adding that they used either stainless steel or galvanized steel for materials because those don’t rust, which can be a hazard in a food plant.
The flooring and equipment placed on it was also designed with the same sanitary strategy to be cleaned from all angles. The flooring includes trench drains and is sloped strategically in high-use areas to avoid pooling water—especially important in a triple-wash processing operation. “Everything that’s on the floor is held an inch-and-a-half off with grout pads. Nothing is sitting flat on the floor, so it’s all cleanable,” notes Lewandoski. Drying areas were also upgraded by converting overhead monorails to round tubing so water can’t pool on it.
While thorough cleaning and sanitation happens daily after each shift, Krbechek says at least once a quarter, the equipment is disassembled and moved to another part of the Taylor Farms campus for deep cleaning. “We actually cook [the parts] in an oven and bake them, so bacteria doesn’t have a chance to survive. Our new factory is designed to get that equipment out the doors easily, get it cleaned, and bring it back inside for reassembly.”
While daily cleaning and sanitation happens on the processing lines between each shift, at least once a quarter the equipment is disassembled and moved to another part of the campus for high-heat deep cleaning to ensure food safety.Dennis Group
The plant is segregated into hygienic zones called high care, and low care. High care is processing through packaging, and low care is in-between those steps, when product is received from the fields, and at the very end for shipping. If a worker is preparing to start a shift in a high-care area, they’re automatically funneled to that space. “On top of that,” says Krbechek, “we have key readers for the doors now, so someone’s ID badge will predetermine which rooms they can go into, and which ones they can’t, so that adds a layer of safety.”
Production Efficiencies
Because the fire wiped out the entire processing area, Taylor Farms started over with a complete reconfiguration of its production lines to maximize efficiencies and use of space within that 60,000-sq-ft area. The result is a 50% increase in productivity compared to before the fire, with 15 dual-wash processing lines currently in place, that eventually feed into 22 bagger systems, and out to integrated robotics to do the heavy lifting and save labor.
Taylor Farms reconfigured its production to feature 15 dual-wash processing lines, resulting in a 50% increase in productivity compared to the previous setup.Taylor Farms
“Before, the lines were in place and we added on to them as the company grew,” notes Krbechek. “We have reorganized now to have very clear, linear processing lines with higher throughput and more consistent feeding of product into them, so it’s more efficient from start to finish—our operators can see the entire process now and make sure the machines are running in top form. Before, it was more difficult to see where a bottleneck was happening or the source of a slowdown. With this layout now, it’s a nice streamline, and we’re laid out with extra room and flexibility for growth and to add new technology in the future.”
Sustainability
Several eco-friendly and resource-saving initiatives were included in the new building and in the production process. Water conservation was a primary goal for Taylor Farms, so the company installed a highly efficient refrigeration system that uses 20% less water than before.
“We added an energy-saving device to pre-chill our inbound city water which saves millions of BTUs,” Krbechek explains. This innovation not only reduces the environmental impact of the plant but also lowers operational costs, contributing to the overall sustainability of the facility.
Overhead monorails in the drying area were converted to round tubing to prevent excess water from pooling above.Taylor Farms
The water that Taylor Farms uses to triple-wash its leafy greens is part of a circular system that results in water reuse in Salinas. “That water goes to a specialized municipal treatment system that the city of Salinas has, and then that water gets pumped back into the aquifer. Farmers will eventually draw that water back out into the fields, so we have a complete circuit for our water use,” Krbechek says.
![]() | Find out how frozen-pea processor Foodhills increased yield by investing in technology. |
Other areas of the plant where energy savings was enhanced include increased insulation in the building envelope, which helps lower daily energy usage to keep the structure consistently cool; power-saving LED lights were installed throughout; and variable-frequency drives were added to fan coil motors. “Those fans ramp up and down based on need instead of just roaring at full speed all the time,” says Krbechek. “That gives us a twofold advantage. We save on power usage, but it also helps our employees because the sound is not as loud, and it makes for a better work environment.”
Interstitial Space
The fire destroyed the MCC (motor control center) room where all the power and utility equipment that provided energy to the plant was located. In rebuilding the facility, Taylor Farms replaced the MCC space with an inviting public viewing area overlooking the production floor, where visitors and staff can watch product processing in real-time through a long line of large windows.
Here you see construction on what would become the interstitial space between the roof above, and the processing plant below. This is where Taylor Farms houses its motor control center, where all equipment that powers the facility is located.Dennis Group
To house a new MCC room, Taylor Farms created a large interstitial space between the rooftop and the production room to place all the new power equipment, and nine miles of overlapping piping connected to those units. This new space is air conditioned, eliminating condensation—which mitigates a potential food safety hazard—and provides a buffer from the heat of the utility equipment and the rooftop above, allowing the temperature on the production floor to stay consistently cool.
“There’s a tremendous amount of heat from the control panels, so we added ammonia refrigeration into our interstitial space to take out that heat,” says Krbechek. “That’s advice I would offer for any new factory construction: build a proper interstitial space, keep it air conditioned, and leave enough room to handle future growth.”
Flooding and Supply Chain Challenges
Post-pandemic facility construction remains fraught with supply chain challenges, particularly when it comes to securing materials on time. Taylor Farms’ project was no exception, as the original plans needed to be modified to accommodate delays and shortages for items like steel beams and transformers, but still stay on a strict one-year timeline for completion.
“We couldn’t get the most common electrical items—anything that was power driven,” remembers Lewandoski. “Switchgear availability was more than a year out, and we didn’t have that kind of time. We found refurbished switchgear that we could get in six weeks, so that’s what we used. We just had to adapt our plans to the reality of the situation.”
The rebuilt Taylor Farms plant in Salinas produces triple-washed leafy greens in volume for foodservice customers.Dennis Group
As if the supply chain headaches weren’t enough, California was hit with historic flooding last year via a weather event called an atmospheric river, and Salinas was
“Every day we were getting rain, but we couldn’t stop [construction], so we had to get creative,” Lewandoski says. “We had to dewater and demuck the site, and we had to bring in stone instead of dirt to fill the low spots on the site, which is more expensive, but we couldn’t stop working.”
Full-Circle Commitment
The Taylor Farms foodservice plant in Salinas employs approximately 1,000 workers, and even though staff had no work right after the fire, the company still provided a month’s pay for them while plans were crafted to rebuild.
That goodwill toward workers continued through the amenities that were added to the new plant with larger entry spaces, washrooms, lockers, and shift preparation areas. There’s also a separate two-story employee services building that was built as part of the overall project plans for Taylor Farms, which houses brand-new offices, and an expansive break area with high ceilings, large windows, and indoor/outdoor seating.
Just a few days after the fire, company CEO Bruce Taylor set a bold deadline for completing the rebuild. And just to reinforce that commitment to the surrounding community, a billboard was put up on the side of the road leading to the plant that announced Taylor Farms in Salinas would be back in exactly one year, April 2023—an ambitious goal at the time.
“I came out to the site a week after the fire, and at that point, we didn’t have a detailed plan for rebuilding yet,” remembers Lewandoski. “Coming in, I see a billboard on the road that says Taylor Farms will be back in April 2023. I stopped and took a photo, and when I met with [Krbechek] that day I said, ‘Hey, I appreciate the confidence, but what are we doing?’ And he replied, ‘We’re going to the moon, and we’re going to land.’ That was the mindset that carried this project through in one year.”
A mural on the side of Taylor Farms’ rebuilt Salinas facility emphasizes the company’s teamwork and commitment to the surrounding community.Aaron Hand
See The 2024 Manufacturing Innovation Award Winner at PACK EXPO International
ProFood World’s eighth annual Manufacturing Innovation Awards is scheduled for Tuesday, Nov. 5, at 4 p.m. on the Processing Innovation Stage at PACK EXPO International in Chicago.
Here are the 2024 finalists:
· Riverbend Ranch—A greenfield Angus beef processing facility built adjacent to the ranch’s feedlots just outside Idaho Falls, Idaho, enables cattle to be walked over for humane, state-of-the-art processing.
· Taylor Farms—When a devastating fire destroyed the 60,000-sq-ft production space in this Salinas, Calif., produce facility, Taylor Farms rebounded and rebuild better than ever on a tight deadline.
· Hill’s Pet Nutrition—This 366,850-sq-ft pet food plant in Tonganoxie, Kan., was envisioned as a smart factory fully leveraging automated technology, data collection, and sustainable building and process systems.
Hear more details about all three projects on Nov. 5 at PACK EXPO International, and find out who wins first prize. For more information or to register for the show, visit packexpointernational.com.