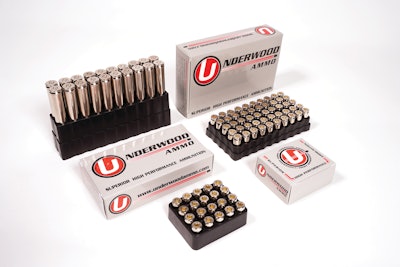
Kevin Underwood first hung out a shingle for his company, Underwood Ammo, in 2013 after recognizing he could fill a gap in the market for better ammunition at a reasonable price. Since then, the brand has parlayed the quality of its product into a premium reputation, and now some of the world’s leading target shooters and hunters, as well as law enforcement and military, swear by the ammunition. And they’re willing to tell their friends and peers about it.
But like many newer brands, regardless of industry, that are making ultra-premium products at lower initial volumes, Underwood Ammo didn’t start out with a heavily automated, lights out-style facility. That was particularly true of the packaging piece. As recently as a year ago, most packaging operations, including cartoning, labeling, and case packing, at the ammunition company’s Sparta, Ill., headquarters was done entirely by hand. Some automation was in place for placing rounds of ammunition into injection-molded plastic trays via an Ammo Tray Loading Machine (ATLM), and operators used an automatic case taper for closing corrugated shippers, but that was about it. Meanwhile, the brand’s growing popularity created a demand that, considering the limited availability and high cost of labor, could only be met with automation.
When assessing how to address packaging automation, Kevin Underwood wasn’t looking one year or even five years down the road. He was looking at the big picture and preparing to scale. So, he didn’t bother with an intermediate or semi-automatic installation, opting to go from zero automation to a system that’s virtually future proof. The fully automated custom monobloc cartoning, case packing, and palletizing system at Underwood Ammo.
“We’re skipping a few steps, but it means we won’t have to do something more than once. …That’s pretty much how I work,” Underwood jokes.
With that attitude, it wasn’t any surprise to his team that Underwood’s first foray into integrated packaging machinery was directly into fully automated equipment from Aagard, diving right into the deep end. The custom project for secondary packaging in a small-footprint monobloc enclosure includes a cartoner, a case packer, and a palletizer, plus coding and marking, vision, and more.
The monobloc system maintains the smallest possible footprint by eliminating the wasted space associated with separate machines for each of the cartoning, case packing, and palletizing operations, obviating the long handoffs between each. Plus, it allows changeovers to happen with a single HMI input instead of three.
“The rounds are put into trays automatically for the most part with the ATLM, so our biggest bottleneck was [downstream of] that, in packaging,” Underwood says. “We’ve been trying to automate as we go, so we just keep moving down the line. Aagard was the last piece of the puzzle, and we obviously stepped really far forward by going to this much automation and sophistication.”
Infeed and erecting
Trays of ammunition coming off the ATLM are placed in roller carts, then introduced to the Aagard equipment by hand. This signals room for future automation, but more on that later. Infeed is two-up, with two parallel single-filed lanes of trayed ammunition, oriented lengthwise, being conveyed into the cartoning equipment. Given the manual or semi-automatic state of upstream operations, inspection via Cognex vision and scanning systems immediately takes place. A two-up ammunition tray infeed configuration allows for double the production at a moderate, manageable pace.
“One of the great things Kevin [Underwood] did brilliantly at the beginning of this project was targeting it to be way over capacity. And then, he understood that some of the processes to date, at least until they reach their future state, are semi-automated. There’s an opportunity for a cartridge [of ammunition] to be missing from a tray; sometimes that can just happen,” says Eli Jeffers, supervisor at Underwood Ammo. “So, we went ahead and put inspection on the infeed. We visually inspect trays with a camera, identify when [a missed round in a tray] is the case, and then track it through the system and reject it to make sure that it doesn’t go out to a customer. The last thing that you want is for a customer to be shorted; when this is a premium product, they don’t want to receive a partial tray. We put in extra effort there.”
In another example of Underwood planning ahead, he was already introducing “pull-down” to the system early in the project. This was evident in his opting for a two-up or dual infeed for trays of ammunition, as well as a two-up infeed for erecting paperboard cartons from 2D blanks. The idea in both cases was to increase the overall capacity, while keeping rates slow and manageable. This two-up approach effectively halves the rate for individual lanes. Each lane performs 25 cycles/min, but with a two-up format, Underwood gets the benefit of a 50- carton/min capacity. Trayed ammunition is laid prostrate for carton loading.
“That’s just goes along with Aagard’s philosophy to create the smoothest possible motion,” says Jonas Capistrant, applications engineer manager, Aagard.
It was also convenient to have two infeed conveyors, since such a layout increased the amount of space that operators could use to load trays of ammunition as they were placed on infeed conveyors from upstream operations.
“Our goal was both to fix the bottleneck now and the one in the future that we haven’t even gotten to yet,” Underwood says.
Paperboard cartons are introduced to the system via two parallel magazines filled with 2D flat blanks. The company uses tuck tab-style, reclosable cartons instead of full adhesive flap closing, so the end consumer can conveniently reclose the cartons after they load individual rounds of ammunition. Cartons are mechanically erected, via opposing-cup vacuum grippers, into 3D cartons with tuck tab flaps both facing down as they’re loaded into two parallel flights, then carried downstream consecutively.
“One of the things that’s very common in the industry is for tuck tab flaps to oppose one another. And originally, that’s the format they were planning on here, where you tuck one flap upward, and the opposing flap downward,” Capistrant says. “But for the purposes of automation, it’s easier if both tuck tab flaps are down and on the same side, so that they aren’t in the way when we’re loading the ammunition trays or later on when we go to tuck that flap. We don’t want to tuck the tab into the plastic tray, we want it to go effortlessly into the carton. So, we made a change to the carton for the flaps to be on the same side instead of opposing each other.”
Another unique element of the carton-erecting configuration is the practice of removing blanks from the magazines oriented lengthwise, then using the mechanical end effector to rotate them widthwise into the conveyor flights, with tuck tab flaps splayed outward. Sensors recognize empty tray slots.
“The original design, even at the time of sale, was that we were going to do something more traditional, where we stood the cartons up on-end in the magazine. But they don’t hand-load into the magazine as easily that way,” Capistrant says. “So, we added a feature where we load the blanks in the way that’s best for loading, which is lengthwise. Then we rotate the blanks as we erect them, and they are placed into the flights, giving us the best of both worlds. They’re in their most stable form when loaded and also in the right format as they’re conveyed downstream through the machine.”
Carton loading
The paperboard cartons themselves, which are supplied by Graphic Packaging International (GPI), are 24-pt thickness KD blanks with the manufacturer’s (side) flap pre-glued, making for the only adhesive in the primary packaging portion of the system. The paperboard cartons are one-side printed and use an extra UV coating for improved shelf impact.
“We want our packaging to be premium, as well as the ammunition,” Underwood says of the sturdy, slickly decorated cartons. The 2D carton blanks reside in magazines oriented lengthwise, then pivot 90 deg during erecting to enter the flights widthwise, with both tuck tab flaps facing downward.
Back on the packaging line, as erected cartons travel down the line toward carton loading, the two down-facing tuck tab flaps are each subducted under a metal flange. This pre-tucking station keeps the flaps from interfering with ammunition loading into the carton downstream.
Meanwhile, the trays of ammunition on the product infeed are rotated 90 deg to lay on their side, with the plastic trays facing downstream and the narrower, bullet ends of the rounds facing upstream. Next, they are gently loaded into the cartons by a pusher.
“Again, this is why we changed the whole design to have the tuck tab flaps facing down,” Capistrant says. “We’re protecting those flaps [by subducting them under the metal flange], and a funnel loader protects the carton’s corners, preventing either the plastic tray or even the ammunition cartridges from catching the edge of the carton. It’s very intentional the way it’s set up at the load station that the trays of ammunition have a free and clear path to get into the carton.
“When closing, we wanted the tuck tabs to tuck into the carton above the trays,” he continues. “Gravity is holding them down, and the tuck tab penetrates into the carton by about one inch when they’re closed.”
By tucking the tab over the prostrate plastic tray, instead of trying to drive the tab under the heavy tray where it lays, the contents of the carton don’t interfere with carton closing of the tuck tab flaps. These flaps are closed using Festo pneumatics. Tuck tab flaps are subducted under a metal flange after erecting for easier loading of trays of ammunition.
This another instance where the two-up infeed format again comes into play. Underwood is investing in well-decorated paperboard material, so smooth, slower operation that carefully protects the carton and gently loads the trays of ammunition prevents unsightly damage to the premium primary package.
Loaded cartons with tuck tabs closed are then coded and marked with a Videojet inkjet system. Variable data includes the ammunition caliber, weight of the round, a description of the round type, a lot number, and a UPC code.
Closed cartons are generally cross-pushed out of a single-file chamber into a tipper, where they are stacked into 2x5 formats of 10 cartons. Then cartons are tipped onto their edges by rotating them 90 deg. Underwood notes that most formats adhere to this 2x5 pattern, but there’s flexibility for different patterns in the future.
Tipping on the edge doesn’t accomplish any specific function for the cartons, it was simply an orientation requirement; it worked better with the machine layout and the way in which the machine erects cases. A mechanism in the tipper applies pressure to the two stacks of five cartons to snug them together, provide three-sided containment, and eliminate extra play between the cartons prior to case packing.
Fully automated changeover
For the purposes of a machine walkthrough, we have so far focused on a few specific SKUs of 2x10 or 4x5 arrangements of 20-ct ammunition in injection-molded trays. But the company also does 5x10 formats for a 50 ct and a smaller 10 ct of ammunition. But most important, all these formats are available in many different ammunition calibers and round types. That translates into 350 different SKUs that are being packaged into the 10 different carton styles currently programmed into the machine. As they grow into this equipment, Jeffers expects to program as many as 35 different recipes for 35 different discrete pack formats. Trays of ammunition from the two-up infeed are oriented to lay on their sides before pushers load them into cartons.
Any way you slice it, the product mix is immense, and changeovers are frequent. That’s why Underwood went with an optional feature, a fully automated changeover.
“Best money I ever spent,” Underwood says. “I can hit a button, and it changes over 96% of the machine, and it has absolutely done exactly what we hoped. The changeover time is minimal at less than 10 minutes. It’s obviously an expensive option, but it was worth it. … Our industry has actually slowed down a little bit. We’re not running [long runs of single SKUs] gangbusters like we were, so changeovers are even more important [for shorter runs with more mix]. It’s been phenomenal from that perspective.”
A less frequently discussed element of automatic changeover capability is how easily a CPG can program in and test their own recipes—this as opposed to relying on the OEM to do all programming at the outset of the project, or more expensively, via aftermarket support.
“If they had wanted us to test all 35 of their recipes, that would have been very involved for us. So, we made it so that they could set up their own sizes without Aagard technicians’ help. It was a little bit of a learning curve at the start, but now they’re setting up recipes we don’t know about,” Capistrant says. Cartons are formatted to 2x5 stacks, then oriented by turning 90 deg on-edge, prior to three-sided containment and a pusher loading them into a corrugated case.
Adds Jeffers, “It’s very easy. I actually set up a new one this morning, and the total process took me 20 minutes all the way through, with just some minor tweaking here and there, changing offsets by millimeters. Once I get all the heights and widths programmed in perfectly with normal rejection, it could take about 30 minutes max, from start to finish. And once it’s in there, it’s permanent. I can hit that recipe a year from now, and the work is already done.”
“This is a feature we call Rapid Launch, our machine technology that allows our customers to set up a new product in minutes, versus retrofitting the equipment or installing another line,” says Capistrant.
Case packing and dual-bay palletizing
Speaking of SKU proliferation, case-packing operations on the monobloc were designed to erect and pack corrugated cases that could accommodate a range of product, from cartons of 8-in.- long rifle ammunition to comparatively short pistol ammunition.
“A typical flight-in case packer doesn’t support that wide of a range very well,” Capistrant says. “We actually designed a unique, overhead-shuttle case-packaging configuration where we can achieve solid opposing-cup erecting out of the corrugated case magazine, load it, and be able to handle that very large case range from a very shallow case that’s not typically supported by flights, all the way to the larger formats.” Corrugated cases are packed, closed with hot melt equipment, and printed via inkjet with variable data before palletizing.
Magazines containing 2D corrugated case blanks are situated beneath case-erecting operations. Operators can easily refill magazines, despite blank-picking and -erecting operations above them, thanks to careful containment and safety measures. The monobloc machine format creates physical barriers between operators and the moving components.
Cases are closed and sealed via hot melt adhesive equipment from Nordson, and slid through another round of coding and marking. In this operation, two facing Videojet inkjet printer heads print the same variable data that was printed onto the primary package, this time onto the corrugated. Cases are then taken directly off the end of the case packer and printer and are transported by overhead shuttle into a dual-bay palletizer. Because of the medium-paced pallet rates, new pallet loading doesn’t happen as frequently as it might in higher-speed operations (yet, at least). Automated pallet dispensers and slip-sheet inserters aren’t required at this point, reducing system cost.
The dual-bay setup with overhead-shuttle case transport and fully enclosed bays allows an operator plenty of time to remove a full pallet and move it to stretch wrapping via Orion equipment, while the system continues to build out a pack pattern for the second pallet in the second bay. Though the cases are transported overhead by vacuum suction shuttles, special attention to operator containment in both pallet bays allows for safe operator entry into the bays to retrieve filled pallets, just as was the case when case erecting was happening above the corrugated blank magazines. The machine slides a physical barrier between moving operations and the operators. Corrugated cases are packed, closed with hot melt equipment, and printed via inkjet with variable data before palletizing.
“We’re singulating the cases as we place them on the pallet, so there is a lot of flexibility of pallet pattern and how we place them on the pallets. It even has the capability to do pinwheel patterns,” Capistrant says. “These pallets are quite heavy, so they weight-out before they size-out, and that gives us lots of options.”
For the entire packaging system, automation componentry, including motors, drives, PLC, and HMI, are all from Rockwell Automation.
Results and what’s next
Once the monobloc packaging system was up and running, Underwood was able to reallocate labor away from the tedious, repetitive, and ergonomically unfriendly packaging operations and place them in more useful roles elsewhere in the facility.
“It’s just a massive labor savings in packaging operations, and it was a job nobody wanted to do,” Underwood shares. “They could pack a box pretty fast, but it didn’t look fun.” Cases are singulated and palletized by an overhead shuttle, after coding and marking directly onto the corrugated. The products’ weight tends to keep pallet heights low, but many pallet patterns, including pinwheel, are available.
The new packaging equipment also allowed Underwood and Jeffers to refocus attention on the upstream traying operations, giving them more human hours to help accumulate trays and build a backlog of trayed ammunition to keep the Aagard beast fed. But that only brings into sharper relief the fact that huge leaps in automation like this one only shift the bottleneck to somewhere else on the line. And that bottleneck now is in the traying operations, both manual and on the ATLMs.
“A faster, automated traying machine that will be directly tied in with the Aagard, that’s what’s next,” Underwood says. “We’re feeding this machine by hand, but the intention is for that to eventually be a seamless process.”
And it almost certainly will happen soon, perhaps even in a new building—Underwood is almost out of space in his current facility. He has already purchased the property, and plans are in the works. Regardless of where on the line it happens, more and better automation in traying and elsewhere is needed to get the most out of the new Aagard packaging automation. A dual-bay pallet format means that palletization in a second bay keeps right on going while operators remove the pallet from a first bay. The machine isolates operators from any moving parts with a physical barrier for safety.
But that has been Underwood’s plan all along: to future-proof by scaling up operations far more than is called for by the current needs of the day. This will allow Underwood Ammo to grow into equipment over time and avoid the stepwise, incremental ramp up that slows progress.
“One last great part of our experience with Aagard has been their service and their warranty department,” Underwood concludes. “They’ve really taken care of us on anything we’ve had an issue with. They’ve always been right there by overnighting parts, and if I’ve had any kinds of questions, I’ve always just been able to text somebody, and they’d respond right away. It’s an impressive finishing touch on a successful installation.” -PW