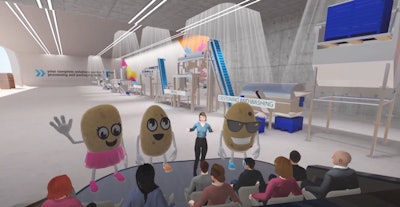
At PACK EXPO Las Vegas, tna solutions was offering visitors a chance to step into a virtual factory, getting a taste of how digital twins can change the way production environments are approached.
Once I got situated in the tna booth, the company’s representatives sat me down, outfitted me with a virtual reality (VR) headset, and sent me off to their metaverse, where cartoon potatoes willingly subjected themselves to peeling, slicing, and other processing steps. The interactive experience was just an entertaining representation of what’s possible with tna’s Virtual Factory, notes Natasha Avelange, global extended reality manager for tna solutions.
The Virtual Factory leverages extended reality (XR) to enable remote planning, scoping and testing of production lines, installation and maintenance, reducing carbon footprint and downtime. It provides a fully functioning and interactive digital twin of any planned or current operations.
“We basically create one whole model of all the equipment, all the utilities, the building—and customers can meet our team in that world,” Avelange says. “Whether it’s on a headset, on a laptop, or on a phone, it’s the next level from having only drawings to look at and even 3D models.”
Though 3D models have become increasingly popular to better plan new facilities and production lines, the XR technology helps customers better immerse themselves into the future factory. “When you plan a new factory or a new process line, three-dimensional drawings help already, but one of the challenges for customers is: How is the accessibility of the equipment? Can the operator move around the equipment?” notes Eric Geling, chief sales officer for tna solutions. “Before you actually build the facility, you can step away from the traditional 2D or later 3D layout drawings that you would do for a project and say, ‘OK, this is your plant, actually.’”