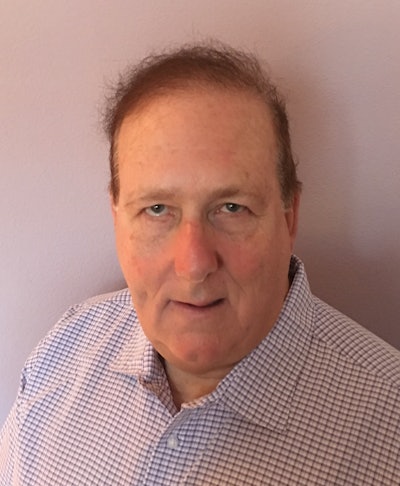
The consumer packaged goods (CPG) and food manufacturing industries are under more pressure than ever to respond to business demands, such as:
- Increased capacity.
- Speed to market.
- New technology introduction.
- Making more with less.
- Leveraging capital budgets.
In this ever-tightening, resource-constrained environment, why is it more essential than ever to properly plan for and execute factory acceptance tests (FATs)? Don’t FATs cost extra time, money and product waste? Isn’t my contract with the OEM or my design firm going to assure me that the new equipment works? Unfortunately, the reality is the absence of an FAT or a poorly prepared one can significantly delay a startup, increase costs and cause numerous ongoing operational issues. Significant time and expertise is lost when issues arise on the job site when technical solutions or quality cannot be easily fixed at the factory.
Another factor is that most contracts specify that passing an FAT is a criterion for payment. Purchase orders or contract terms are derived from the functional requirement document. It is important that this test be witnessed by a technically competent project manager with operational knowledge or owner representative to ensure compliance.
Being part of an entrepreneurial startup company is exciting, challenging, invigorating and, at times, overwhelming. Impossible Foods is an innovative food technology company with a strong scientific and manufacturing knowledge base. However, limited staff resources or time constraints to meet project timelines does not mean FATs should be avoided to execute a project more quickly. Just as there are protocols for proving a science or experimental thesis, it is also important to use similar due diligence for the factory acceptance process.
I participated on the OpX Leadership Network team that published the document “One Voice Factory Acceptance Tests: Protocols for Capital Equipment in the CPG Industry” in late 2015. I can attest to the value of FATs. When properly planned and executed, FATs provide benefits that far outweigh the costs. Two overriding benefits are vertical startups and sustainable operational reliability.
It all adds up
Do the math on vertical startups. How much would it mean to your business to give back an extra week or two in production? Most managers agree there are ways that you can significantly compress the traditional ramp-up time of a new production line without increasing the size of your team or suppliers’ workloads. Consider how much cost is associated to wasted on-site labor.
Startups are the tip of the iceberg. The reoccurring value is earned through sustainable operational reliability. You can use the OpX Total Cost of Ownership model and Overall Operational Effectiveness Benefit Calculator to assist you in quantifying this benefit to the business. Engagement of the workforce (also an OpX best practice) begins this positive cycle of sustainable operational reliability.
FATs are terrific opportunities to engage the many different stakeholders impacted when bringing in a new manufacturing line. Soliciting opinions and concerns during the design phase, providing hands-on experience during the FAT, training in operational nuances, and participating in the new equipment installation process will create a sense of ownership.
First and foremost, the FAT protocol is a tool to engage in a dialogue with key stakeholders. Typical questions should include:
- What is critical to ensure the project’s success?
- What does purchasing, operations, engineering or maintenance need?
- What does the OEM need, and when does it need it?
During my career, I have led numerous FATs. Some more successful than others. Failures were often due to rushed fabrication with incomplete checkouts by the vendor. The OpX tool on FATs is beneficial to both the CPG company and equipment vendor.
When I arrived at Impossible Foods, a major project was just completed by a design-build firm with an FAT on major equipment. The complex project of starting a new production line was successfully implemented. My role in the organization is to expand this production capability to other sites to meet our growing demand. I ensure proprietary designs are properly developed, operational technology is utilized, and the FAT protocols and the many other OpX best practices are systemically applied. According to Steve Schlegel, managing director of PMMI’s OpX Leadership Network, “CPGs adopting the OpX best practices in their business will reap the benefits of accelerated business results.”
You may wonder if the FAT protocol document is needed on every project. The answer is no, but the process is. The more complex or custom the project or situation, the greater the value is derived from an in-depth review of the FAT protocol. For a more standard purchase with little risk to your startup, the team may decide that doing an FAT via FaceTime or video is all that is required to certify that you will receive what you have purchased.
The importance of user acceptance testing is essential to the successful implementation of your project. Usually all staff are stretched to the limit during a startup. Following the FAT process will avoid additional coordination and time spent on solving equipment startup issues. In the resource-constrained world of capital expenditures, using both the FAT process and OpX best practices can significantly increase your project’s success.
For more information, visit www.opxleadershipnetwork.org.