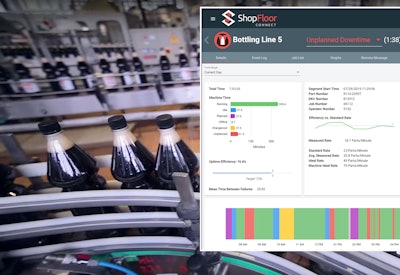
This content was written and submitted by the supplier. It has only been modified to comply with this publication’s space and style.
Wintriss also previewed a new ShopFloorConnect interface that is planned for 2024. Advanced ShopFloorConnect OEE and Data Collection Software collects downtime and production efficiency data from every machine, in a variety of industries, including packaging, food, beverage, discrete manufacturing, metal forming, and metal fabrication. Data are displayed real-time, and indispensable manufacturing reports are produced, including detailed OEE reports in a variety of formats.
Attendees were especially interested in how data are collected, including how to minimize, or in some cases remove, operator involvement in the collection process. “Traditionally, a ShopFloor Connect Machine Interface (SMI2) is installed on each machine, featuring a touch-screen display that allows the machine operator to select downtime reasons and enter data,” said Jim Finnerty, Product Manager, Wintriss Controls Group. “In 2024, we will be introducing an innovative and cost-effective alternative to the SMI2, which will provide seamless automation with no operator input required.” The company also reports that additional analog/ digital inputs that can be customized will be added to the new interface.
The latest functionality in ShopFloorConnect gives packaging and processing professionals efficient and easy-to-use software for increased productivity and reduced machine downtime, including when remote monitoring is required. The software can significantly increase manufacturing capacity and profitability by identifying and quantifying excessive production losses and bottlenecks. An interesting demonstration at the show, attendees saw how the SMI2 interface communicates and integrates data collected from a conveyor belt production process and how the information is used and reported on for continuous improvement initiatives.
Wintriss also highlighted the new ShopFloorConnect PM Tracker that enables users to track important machine preventative maintenance (PM) items by run-hours or machine cycles, issues targeted alerts when an item requires PM, and tracks the maintenance work history for all machines.