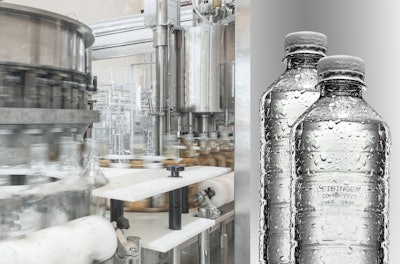
This content was written and submitted by the supplier. It has only been modified to comply with this publication’s space and style.
LEIBINGER, a developer of coding & marking technology, understands its customers’ requirements and responds with exceptionally efficient solutions. This includes the advanced air dryer feature, which counteracts high humidity and extreme temperatures to ensure the best printing results in challenging production environments.
High humidity and high temperatures aren't only found in tropical and subtropical climate zones, such as Southeast Asia. These extreme conditions are also often encountered in many production environments such as those in the Beverage, Food and Packaging sectors. LEIBINGER has developed an outstanding ink portfolio that can easily deal with these challenging production environments. However, there are applications and production processes where the ambient conditions impact on the inks’ processing and adhesion properties. Examples of this include food that is pre-cooked and filled during production, or printing cables in areas with high humidity and temperatures. Together with its customers, LEIBINGER has taken a closer look at these challenges and developed a solution to ensure maximum coding & marking efficiency and reliability.
The air dryer effectively counteracts humidity
Continuous inkjet printers (CIJ) use a continuous ink jet to print best-before dates, texts, codes or other markings. Conventional printers can cause condensation on the print head if the humidity is very high. Humidity can also affect both the inks’ viscosity and drying time. A solution developed by LEIBINGER with an integrated air dryer prevents this from happening and guarantees the inks’ adhesion and rapid drying—along with seamless, smooth operation.
This is how the air dryer works
In short, the LEIBINGER air dryer draws in the humid ambient air, removes the moisture from it and directs the resulting dry air into the print head. This ensures a dry environment in the print head, in contrast to the surrounding production environment.
Identifying and meeting market requirements
“As a leading international coding and marking specialist, we listen closely to our customers and develop solutions to support them in their day-to-day operations. This is exactly how the air dryer feature originated. Under extreme ambient conditions, it ensures that CIJ printers can reliably deliver the best possible print results at all times, including high print adhesion,” explains Alexander Deuchert, Head of Product Management at LEIBINGER.
Thanks to its full-coverage global service network, LEIBINGER always has its ear to the ground. Deuchert highlights: “Our service technicians advise customers on all continents. Together with the production manager, they determine on site which printer specifications, options and features are best suited to the customer’s application—including whether the integration of an air dryer is recommended for successful operation. This option can also be retrofitted to existing printers and LEIBINGER’s qualified service team is also happy to provide support in this regard."