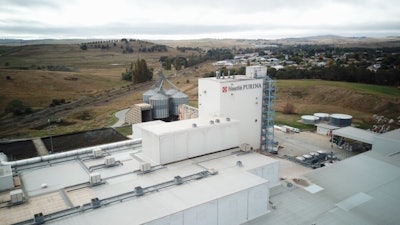
Nestlé has unveiled a $90 million upgrade, including new state-of-the-art high-speed manufacturing technology, to its Blayney, Australia, site to expand Nestlé Purina PetCare petfood production to meet the growing demand for wet cat food in the country. It will allow the company to scale up production of single-serve wet cat food by over 120%.
The upgrade brings Nestlé’s total investment in the factory to more than $200 million. Opened in late 2014, the wet cat food facility was developed to create premium products with the taste profile cats prefer and the simplicity their owners prefer. The expansion will position Nestlé Purina as a key regional supplier, with both wet and dry petfood exported from Blayney to New Zealand, Thailand, and Japan.
The site also will see a significant quantity of local ingredients used in production, with more than 85% of the raw materials, including meats and grains, used at the Blayney factory being sourced locally.
![]() | Nestle Investing $675 Million to Build Beverage Factory |
Nestlé Blayney Factory Manager Charlene De Wit says the new facility is a testament to Nestlé’s commitment to local manufacturing and support for the Central West community. “We are proud to produce quality Purina pet food for our much-loved furry friends across Australia and around the region, right here in Blayney.
De Wit continues, “We have an incredibly dedicated and highly skilled team here at Blayney. By bringing leading technology to our factory and continuing to use high quality ingredients in our product, we are even more confident that we will continue to enrich the lives of pets and the people who love them for years to come.”