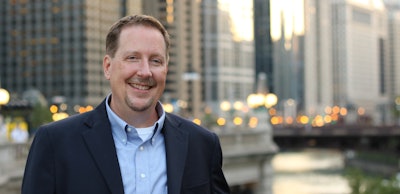
Automation is such a broad term. It can mean many things to many people, and its connotation can change vastly depending on time and circumstance. Perhaps it was my recent visit to PACK EXPO East in Philadelphia or maybe it has more to do with a general movement in this direction, but I’ve been reminded lately that automation does not have to be the huge undertaking that many people might think of when faced with the prospect of starting such a project.
We could talk about whether or not automation takes workers’ jobs—a relevant conversation whether the project is large or small—but we can save that discussion for another day. Any level of automation will likely reduce the number of people needed for a particular task, which is essential amid the workforce turmoil industry faces these days.
It seems that, particularly with the restraints that the COVID-19 pandemic introduced in factories and the extreme workforce challenges being faced, the food and beverage industry is beginning to come to terms with the need to automate. That can be more than a little daunting—and, in some cases, it is admittedly a huge undertaking. But there are all kinds of small steps you can take that will go a long way.
At a recent tour of TopPop Packaging’s current and newly opened plants in New Jersey, I saw how the contract packager is processing alcoholic ice pops for various clients. One stark example showed how much just a bit of automation could change the landscape. On one side of the aisle, they had 16 to 18 people grabbing six of each of the two flavors and placing them into 12-pack boxes. On the other side of the aisle, they had upgraded to machines that served up six of each flavor to just nine workers to do the same job. It not only reduced the workforce needed on that side of the aisle, but also provided them with the social distancing needed in relation to pandemic concerns.