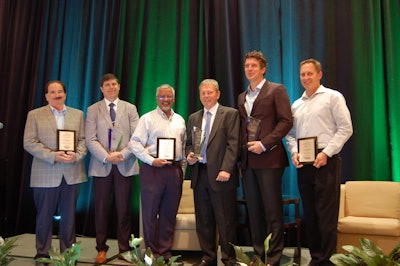
ProFood World honored the best of the best in food and beverage processing at its inaugural ProFood Live! conference June 21 in Itasca, Illinois. The recipients of the 2nd annual Manufacturing Innovation Awards and 6th Annual Sustainability Excellence in Manufacturing Awards shared how they use sophisticated automation, state-of-the-art food safety equipment and innovative eco-friendly tactics to reduce costs, improve product quality and enhance efficiency at their plants.
Manufacturing Innovation Awards
Dairy Farmers of America (DFA) was one of the winners of this year’s Manufacturing Innovation Awards. Wesley Clark, director of processing and technology operations at DFA, told ProFood Live! attendees how its world-class milk drying facility in Garden City, Kansas, uses redundant systems and advanced automation systems to keep its processes running 24/7. The new 267,000-sq-ft facility features the largest single whole milk dryer in North America, high levels of hygienic design, energy-efficient mechanical systems, and a complex automation system to prevent downtime and safeguard against potentially unstable power. DFA also built a 2.5-million-gal wastewater treatment plant that combines the plant’s properly treated effluent discharge with Garden City’s effluent at a shared outfall storage system. This arrangement allows Garden City to provide the combined effluent for the area’s much-needed agricultural irrigation.
Clemens Food Group also won a Manufacturing Innovation Award from ProFood World. The pork processor’s 656,000-sq-ft plant in Coldwater, Michigan, uses highly automated production and material handling systems that are linked throughout the entire facility for a continuous processing stream. Technology such as fully automated laser-guided saws, high-pressure water trim processes, a 3,128-ft Snap Chill chain, and an automated storage and retrieval system enhance worker and food safety while allowing the factory to efficiently produce 12 million lbs of pork per week.
Farmer Brothers received a Manufacturing Innovation Award as well in recognition of the coffee company’s lean, greenfield 127,000-sq-ft facility in North Lake, Texas. In addition to achieving LEED Silver certification, the Farmer Brothers plant features a customized flexible manufacturing system that has led to nearly 95 percent overall equipment effectiveness and reduces the need for human intervention on the floor. It includes advanced roasters that let roast masters operate from a central control room; an automated replenishment optimizer; and custom mixing, weighing and conveying equipment that allow it to respond to rapidly changing market demands.
ProFood World also honored several food manufacturers for their stand-out sustainability programs and projects that prove environmental efforts go hand in hand with profitability.
Sustainability Excellence in Manufacturing Awards: 1st Place Program Category
Snyder’s-Lance earned 1st place in the Sustainability Excellence in Manufacturing Awards’ program category for its wastewater sludge land application program. The snack maker’s facility in Perry, Florida, generated about 5,000 gal of sludge daily. Snyder’s-Lance initially wanted to send it to a landfill, but dewatering the sludge required an intensive amount of chemicals and energy. The company worked with the state Department of Environmental Protection and local farmers to use the wet material for land application. It only took six months to get the program up and running and didn’t cost Snyder’s Lance anything to implement. The program ultimately reduced operations costs significantly for Snyder’s-Lance while providing valuable fertilizer for local agricultural crops instead of taking up space in a landfill.
Sustainability Excellence in Manufacturing Awards: 2nd Place Program Category
There was a tie for 2nd place in the program category. The Conagra Brands facility in Council Bluffs, Iowa, was recognized for its employee-wide programs to increase recycling and reduce unnecessary water use. By renaming its newly renovated waste dock the Recycling Operations Center, it helped changed employee perception about waste, allowing the company to divert an additional 2,100 tons of waste in 2016. In addition, it’s Leak Stoppers program encouraged employees to identify leaks around the plant, saving 2.1 million gal of water. “These programs are ongoing because so much of it is built into the culture of trying to get to zero waste,” said Bill Latenser, EHS manager for Conagra.
Hormel Foods’ plant in Beloit, Wisconsin, earned the other 2nd place award for its solid waste stream optimization program. The facility conducted an analysis of its landfill and recycling processes, getting feedback from employees and third-party audits. As a result, Hormel identified several opportunities to improve its recycling efforts. For example, the company now recycles the foam pads that come in the shipping containers for its tomatoes. In addition, it recycles its food-contact plastics. Hormel also launched an education awareness campaign to inform its employees about these new initiatives and encourage them to take part in the recycling programs. These cost-neutral programs have resulted in a 20 percent improvement in recycling for the plant. “To take this back to your facilities, it’s pretty straight forward: Involve your entire team. Bring it from the ground floor up,” said David West, purchasing manager for Hormel. “Make it easy and make it convenient. … If your facility is not like that, your employees are not going to try any harder than you are to help them recycle.”
Sustainability Excellence in Manufacturing Awards: 3rd Place Program Category
Smithfield’s plant in Salt Lake City, Utah, won 3rd place in the program category for its plastic wrap savings program. The plastic pallet wrapper Smithfield had been using was wrapping inefficiently for years. By simply repairing and overhauling the machine and implementing a regular maintenance schedule for it, Smithfield has reduced the amount of wrap being used. In one year, the company saved 420 rolls of film, which equals 16,800 lb of solid waste and $15,904.
“Nobody really saw a problem with this machine because the pallets were getting wrapped. They were getting on the trucks. The machine was running,” said Bill Gill, assistant vice president of sustainability at Smithfield. “It just wasn’t set up properly. That’s something at Smithfield we had seen opportunity in. To go look at a piece of equipment in operation and say. ‘Is this really working the way it’s supposed to? Is it being efficient? Is it being productive. Can we make it work better than it does?’”
“Pretty simple project really,” Gill said. “I think even more important than the program itself is the concept of thinking about is this really working the way it’s supposed to, and can we take a closer look?”
Sustainability Excellence in Manufacturing Awards: 1st Place Project Category
In the projects category for the Sustainability Excellence in Manufacturing Awards, Smithfield’s Middlesboro, Kentucky, facility won the 1st place award for reducing the amount of packaging used for its ham steaks. The purchasing team worked with its vendors on new packaging that met production needs while increasing efficiency and minimizing waste. The facility now uses 23 percent less packaging and creates 28 percent more impressions per roll, resulting in fewer changeovers and a cost savings of $170,210. “That’s about 150,000 lb of film that’s not going to landfills anymore just from us and the consumer,” said Justin Tong, purchasing and warehouse supervisor for the Smithfield plant in Middlesboro.
Sustainability Excellence in Manufacturing Awards: 2nd Place Project Category
There was a tie for 2nd place in the projects category. Hiland Dairy Foods was recognized with the 2nd place award for constructing a whey recycling and wastewater treatment facility, which eventually expanded to include other sustainability efforts. Located in Chandler, Oklahoma, the facility features two aeration ponds to microbiologically treat about 250,000 gallons of wastewater daily with aerobic bacteria. The facility also separates water from cottage cheese whey, which can be used as fertilizer. In addition, Hiland recycles its tea bags, which are rich in nitrogen, phosphorous and potassium, as fertilizer as well. Hiland is using the recycled water and fertilizer to revitalize 340 acres of infertile land where the facility is located. Area farmers purchase the harvested crops from that land for feed.
“At Hiland Dairy, we’ve made sustainable investments in taking the three biggest wastes out of the plant and put them into revitalizing the land that was basically ruined through farming practices in the early 1900s and oil well production and reconditioning this land to make it productive,” said David Smith, operations manager for Hiland Dairy.
Keystone Foods also earned 2nd place in the projects category. In 2016, the poultry processor set out to reduce water usage by 30 percent for its Eufaula, Alabama, facility. It was able to achieve its goal by installing water-saving shower heads, reuse system for the vacuum pumps, finishing chiller re-use system and foam reduction mixer for the water reuse system. The facility also removed the shower heads in each cropper that flood the cavity of the birds and reduced the main chiller overflow by nearly 23 million gal a year. These modifications resulted in saving 144 million gal of water and annual savings of more than $1 million.
“We did that fairly easily,” said Shaun Morris, general manager of the Keystone Foods facility in Eufaula. “As most of you talked about today, it was all driven by engagement, employee participation, getting people’s buy-in to do what needed to be done and rolling our sleeves up and going to work.”
Sustainability Excellence in Manufacturing Awards: 3rd Place Project Category
The projects category also saw a tie for 3rd place. Land O’Lakes was recognized for installing baffling into its blast chillers at its Turlock, California, facility. It initially installed the baffling to cool down its pudding product to a specific temperature within four hours to meet critical control points and prevent product waste. But this simple baffling ended up improving air flow in the blast chillers that allowed it to decrease the cooling time by as much as an hour per batch. As a result, the company now runs the chillers about 90-120 min less per day and saves $13,000 in energy costs per year.
“When these baffles were not in place, the air was getting forced out and bouncing off the top of the carts,” said Jeff Gaines, plant manager of the Land O’Lakes facility in Turlock. “We came up with the idea of how can we divert the air down into the product and really stop the short circuiting that was happening.”
The Smithfield Packaged Foods facility in Kinston, North Carolina, also won the 3rd place award. It’s simple yet effective meat recovery project has saved the company about $1 per lb for rendering. When the raw product arrives at the plant, the meat is pumped through pipes into bags. At the end of the production, a large amount of meat is left in these pipes, which are broken down, washed out, collected and sent off to rendering. This meat is never exposed to any environment and could be used if captured. Two workers created a plunger system to remove the residual meat from the pipes and process it the next day.
“For less than 100 bucks and a plunger and a little effort by operations, you’re averaging 631 lb of meat a day. Total pounds in this short snapshot last year is 56,000 lb. Annualized savings of $157,000,” said John Meilinger, assistant engineer for Smithfield plant in Kinston. “It’s amazing.”
If your plant excels at manufacturing or sustainability, then we want to hear about it. ProFood World will soon be accepting applications for the 2018 Manufacturing Innovation Awards and Sustainability Excellence in Manufacturing Awards. The next Manufacturing Innovation Awards and Sustainability Excellence in Manufacturing Awards will be presented at ProFood Tech 2019, which is scheduled for March 26-28, 2019, at Chicago’s McCormick Place. Learn more about ProFood Tech.