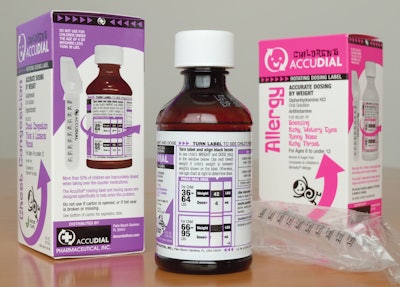
“The revolution in over-the-counter dosing.” That’s how Palm Beach Gardens, FL-based AccuDial Pharmaceutical, Inc. describes its Children’s AccuDial line of liquid OTC (over-the-counter) medications. The “revolution” is the product’s two-part label that allows consumers to administer a precise dose—in milliliters—of a liquid medication based on his or her child’s weight. That differs from many children’s medications that are dosed by age or age groups.
The precise dosing is made possible due to a patented two-part label that utilizes an outer label that “spins.” Primary information (Drug Facts) is displayed on the top label, which also features several windows or clear panels. The inner label is printed with weight in 2-lb increments and the correct dose in milliliters. The consumer turns the label until its window shows the specific weight of the consumer’s child. Below the specific weight is the precise dose amount. The consumer, using an oral syringe that is supplied with every product, draws the precise amount of medication into the oral dosing syringe, which is calibrated to match every weight/dose on the label. The oral syringe comes wrapped in clear plastic film within an outer paperboard carton. (Watch a video about Children’s AccuDial www.accuratedose.com/us_english/product_demo.html)
AccuDial can print 39 different weights with correct dose in milligrams per kilograms. A milligram per kilograms is the dosing method preferred by healthcare professionals, says AccuDial, including pediatricians, nurses, and pharmacists. Because all the weight and dosing information is located on the inner label and the outer (rotating label) contains all the Drug Fact information up to 75% more information to be printed on a 4-oz medication bottle, notes the company.
AccuDial’s Web site notes, “According to the American Medical Association, 72 percent of children are dosed inaccurately with OTC medications.” Both overdosing and underdosing can pose health problems.
‘Spin’ label evolution
Robert Terwilliger, AccuDial’s chairman of the board and chief executive officer, credits Brian Kaplan, MD, for creating the dosing system. Kaplan is the company’s chief medical advisor and director. “In 2000, Doctor Kaplan, a board-certified emergency room physician, had practiced in the ER for nearly 15 years. Over that period of time he treated about 15,000 children who were admitted into the ER for dosing problems. He sought a better way of dosing and eventually developed the idea of the two-part labels.” Terwilliger recalls, “Kaplan met Stephen Key of Spin Labels, who had patented the technology for the outer rotating label. Spin Labels’ ability to provide more label space for printed content on a container provided the answer to Kaplan’s problem.”
The inner and outer polypropylene labels, from different suppliers, are printed by ROI Technologies on a servo-driven 41-inch Bielloni eight-color Central Impression flexo press. The top label is 2.5-mils thick while the base label is 3.8 mils. The gearless press provides registration accuracy, quick changeover, and high-speed production.
“Kaplan held patents on the inner label where we display the child’s weight and correct dose,” says Terwilliger. “We do the calculation and then have the medication information printed onto both labels. We are the only over-the-counter company that is 100-percent consistent in dosing in milliliters and we provide a calibrated oral syringe for consumers so they can properly administer every dose to the child.”
Terwilliger and Kaplan formed AccuDial Pharmaceutical in 2007 and began moving forward with readying the product for commercialization. AccuDial has 17 medications approved by Health Canada sold in Canada for dosing analgesic, allergy, cough and cold medications by weight instead of age.
Aligning packaging sources
AccuDial worked on packaging material selection with Venue Marketing, a graphics design and ad firm that designed the labels and the packaging’s colorful artwork.
Ultra Tech Printing, an integrated firm with in-house graphics, platemaking, printing, and finishing operations, printed the cartons.
Consulting group Empire Emco worked with AccuDial on development, design, advanced engineering, and manufacturing services. Empire Emco manages the blow molds used to make the bottles, the child-proof dosing caps, and the oral syringes.
Says Terwilliger, “We currently own one 14-cavity blow mold for our PET bottles. We are having injection/blow molds made for high-density polyethylene bottles, in 4-, 8-, and 16-ounce sizes. The 8 and 16-ounce sizes will be used for nutritional supplement liquids.”
AccuDial custom-designed the 4-oz bottles that include a “Custom Label Well” where both labels are applied. Bottles are manufactured by Berry Plastics. In addition to the 14-cavity blow mold for the 4-oz PET bottle, AccuDial also owns HDPE injection/blow-molds for 8- and 16-oz bottles. AccuDial is also developing an injection mold for new polypropylene child-proof closures, which will be sourcing through different suppliers.
Spin Labels’ Key explains that the outer label has 13 U.S. patents, along with several foreign patents. “I’m a designer by profession, and I took a concept that I designed in the toy industry to help create more real estate on the container label. It’s been used in different applications, but the AccuDial application represents the perfect marriage of great information at the right time using that technology. With the help of George Michaels at Accraply, we have been able to push the technology forward to where we can make a spin label using high-speed roll-fed labeling equipment.”