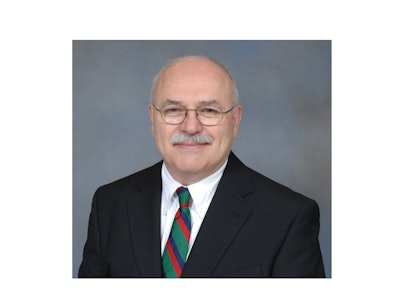
Risk assessment is a process that machinery manufacturers use to identify hazards, evaluate risk and reduce risk to an acceptable level a hazard can cause an accident or incident. Many end users now require risk assessments as part of the procurement process, wanting to ensure they have taken the steps necessary to reduce risk and prevent harmful accidents. Blades, gears, grinders, conveyors, robots, etc., may have hazards that can potentially pose risk to operators and maintenance staffs. Noise and electrical hazards can be problematic as well. In this interview, PMMI’s Director of Technical Services Fred Hayes defines risk assessment and describes the benefits of attending a PMMI Risk Assessment Workshop.
ProFood World: When do most equipment risks happen?
Hayes: Beyond regular operation of the machinery, hazards also occur when operators and maintenance personnel have to stop the machine for changeovers, to clear jams, or to clean or perform routine maintenance. Guards, interlocks, e-stops, alarms, warning labels and manuals for training, etc., are all important risk reduction measures. Even with these risk reduction measures, accidents sometimes may occur. In the event a litigation case results, the OEM (original equipment manufacturer) and the end user can be called into court to prove they were aware of the risks and instituted reasonable risk reduction measures to protect against any harm. Having a documented risk assessment can be extremely valuable in such cases.
PFW: What are the latest risk compliance standards?
Hayes: Risk assessment is required for compliance with the ANSI/PMMI B155.1-2016 standard and for compliance with the EU machinery directive 2006/42/EC. PMMI has expanded the scope of the PMMI Risk Assessment Training Program to include the important issues that generate the most questions from PMMI members and end users.
PFW: What are attendees hoping to learn by attending a PMMI Risk Assessment Workshop?
Hayes: People attended our last workshop at PACK EXPO International 2018 for many reasons. Some were new to risk assessment and wanted to become more involved in safety. One attendee said, “Customers are requesting it, and I want to make sure we’re going down the right path.” A project engineer from a food packaging machinery OEM attended to get a better understanding of risk assessment so he could explain it to his customers. Many come just to make sure they are doing everything the right way. An EE manager from a global OEM said that his company wants to learn how to harmonize safety requirements around the world, and to understand how different customer specs may influence safety efforts.
PFW: Please describe what attendees can expect at a typical PMMI Risk Assessment Workshop.
Hayes: Myself and another trainer, Bruce Main, led the two-day workshop at PACK EXPO International 2018 that touched on CE compliance, global standards, risk assessment basics, legal implications of risk assessment, control systems, etc. But the hands-on portion where attendees can use the Packsafe/designSafe software is where the rubber meets the road. Now in its eighth version, the software guides users to identify various types of hazards, to assess the risks and to develop appropriate risk reduction measures to reduce risk to an acceptable level. The risk assessment process is already in the decision trees. But all choices are editable to fit your particular operation as needed. Sometimes users can get lost in the weeds. The software actually issues a warning if your risk assessment starts to get too ponderous. Participants are able to work on their own projects in the class and walk through a risk assessment. You can actually watch as attendees progress from newbies to having a solid understanding of the ins and outs of risk assessment.
Learn more about risk assessment
For more information on PMMI’s next Risk Assessment Workshop, slated for Las Vegas Sept. 22-23 in conjunction with PACK EXPO Las Vegas, visit oemgo.to/risk.
The course includes:
•Global standards: Why harmonization is important and what standards to use.
•Risk assessment basics: What it is, why do it, the iterative process, how to do a risk assessment and know when you are done.
•Control systems: What to do!
•Legal implications of risk assessment: New equipment and legacy equipment.
•How to deploy risk assessment
The program is open to equipment suppliers and end users. Suppliers who have responsibility for conformance to the ANSI/PMMI B155.1-2011 standard include the manufacturer, manufacturer’s agent, representative or distributor and resellers, installers, modifiers, and rebuilders or integrators of packaging machinery. When the end user performs these functions, it is considered to be a supplier.
Attendees may include engineering managers, engineers and personnel responsible for health and safety, and management safety staff responsible for CE compliance, product safety and productivity.
PMMI also offers in-house risk assessment training for companies that want more staff to get up to speed on the current requirements. “In-house training is where the real issues come out and can be freely discussed. It usually gets really interesting, and is quite effective in getting to practical solutions,” says instructor Bruce Main.
While some may approach risk assessment as an exercise to “check off the box,” instructor Fred Hayes says OEMs who embrace the process design and build better machines.