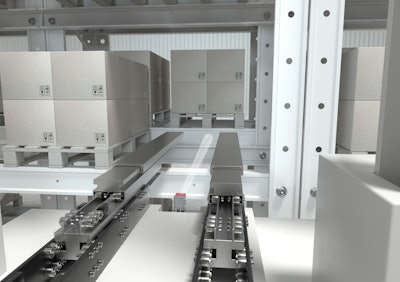
With its camera-based IPS 400i positioning sensor for high-bay storage devices, Leuze electronic—a provider of sensor systems for intralogistics—is expanding its IPS range of products with through this model for optical compartment fine positioning.
About a year ago, Leuze electronic introduced the IPS 200i, the smallest camera-based positioning sensor for single-depth, which is used for single depth pallet high racks and small-part container storage. The IPS400i is made as compact as its sibling to require little space on the high-bay storage device and it detects round holes or reflectors in double-depth bars. This is the design in order to determine the position deviation relative to the target position in the X and Y directions. This should make the IPS 400i positioning sensor particularly suited for use in double-depth pallet high-bay warehouses. A model with integrated heating for use in refrigerated warehouses down to -30 °C is also available.IPS 400i—smallest, camera-based positioning sensor on the market
Both variants—IPS 200i and IPS 400i—are designed to offer the user simple and fast commissioning and operation. The sensors are put into operation using a web-based configuration tool with a user-controlled installation assistant (wizard). Printed configuration codes are meant to be read in without a PC via "Code Generator," which means that configuration adjustments should be made directly on the high-bay storage device. An alignment system consisting of four feedback LEDs further facilitates the commissioning process.
Due to its powerful, ambient-light-independent IR LED lighting, fault-free use in warehouse technology should be possible with a single device for a working range of up to 2400 mm. With the integrated TCP/IP interface and Profinet RT, the IPS 400i is made to be directly integrated into the network environment and enable quick, location-independent diagnostics. Condition monitoring and predictive maintenance are meant to take place using a quality score that detects deterioration in the reading performance of the sensor at an early stage. This is designed to minimize downtime and increase the availability and cost-effectiveness of the systems.