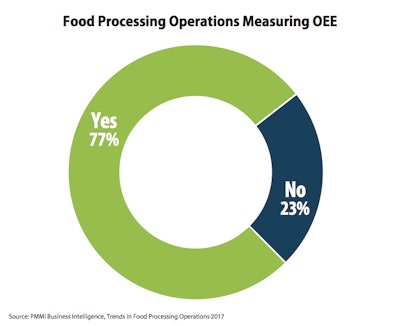
Unlike their peers in pharma, where less than half of operations measure OEE, the vast majority of food processors do measure equipment efficiency, and closely monitor data to make continuous improvements in the plant.
One process engineer from meat/poultry said, “Downtime is usually associated with maintenance problems. There is a need for process machinery with more preventive and predictive schedules and self-diagnosis.”
For food processors, any upstream issue such as blending flow rates, filter changes, roasting times, cooling, sanitation requirements, or slicing inaccuracy can have a negative impact downstream on quality, volume of output, production schedules and product waste.
A senior processing specialist for a cheese company said, “We are looking at proprietary predictive and preventive maintenance programs now to reduce downtime.”
Food processors are looking to OEMs to deliver greater automation, machine flexibility for materials, sizes and shapes, standardized communication platforms, quick changeover, longer pasting parts, and faster serviceable machines.
A director of engineering for shelf goods said this about the complexity, “There needs to be a better synchronization between processing and packaging, with the sharing of formulas and recipes for better labeling efficiencies demanded by a rise in organic, non-GMO and gluten-free products.”
PMMI’s OpX Leadership Network has developed tools to help define and compute OEE, click here.
Source: PMMI Business Intelligence: Trends in Food Processing Operations, 2017.
For more on equipment purchase plans, market segment forecasts, etc., download the entire study here.
Unlike their peers in pharma, where less than half of operations measure OEE, the vast majority of food processors do measure equipment efficiency, and closely monitor data to make continuous improvements in the plant.
One process engineer from meat/poultry said, “Downtime is usually associated with maintenance problems. There is a need for process machinery with more preventive and predictive schedules and self-diagnosis.”
For food processors, any upstream issue such as blending flow rates, filter changes, roasting times, cooling, sanitation requirements, or slicing inaccuracy can have a negative impact downstream on quality, volume of output, production schedules and product waste.
A senior processing specialist for a cheese company said, “We are looking at proprietary predictive and preventive maintenance programs now to reduce downtime.”
Food processors are looking to OEMs to deliver greater automation, machine flexibility for materials, sizes and shapes, standardized communication platforms, quick changeover, longer pasting parts, and faster serviceable machines.
A director of engineering for shelf goods said this about the complexity, “There needs to be a better synchronization between processing and packaging, with the sharing of formulas and recipes for better labeling efficiencies demanded by a rise in organic, non-GMO and gluten-free products.”
PMMI’s OpX Leadership Network has developed tools to help define and compute OEE, click here.
Source: PMMI Business Intelligence: Trends in Food Processing Operations, 2017.
For more on equipment purchase plans, market segment forecasts, etc., download the entire study here.