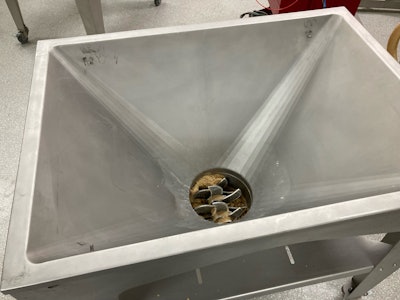
This content was written and submitted by the supplier. It has only been modified to comply with this publication’s space and style.
Lump breakers from process equipment manufacturer Volkmann USA, Bristol, PA, may be quickly and easily retrofit onto a wide range of bulk material handling equipment. Typically retrofit onto bulk bag unloaders, sack tipping stations, and storage silo discharges, the versatile lump breakers enable process engineers to accommodate different materials, particle sizes, and/or changes to humidity and temperature without changing the equipment in the processing line. The lump breakers automatically return materials that have agglomerated in storage to the required particle size and/or cutoff-spec materials down to a target particle size to ensure feeding, conveying, mixing, milling, and other operations flow smoothly in a first in, first out sequence.
Often specified as a companion with the company's pneumatic vacuum conveyors, the stainless steel lump breakers feature a series of rotating blades that quickly transform any lumps into free-flowing powder. From the lump breaker, the powder flows smoothly downstream at a predetermined rate and particle size.
The Volkmann lump breakers are available for retrofit in two standard sizes to meet a wide range of throughput requirements and may be disassembled quickly for cleaning. A choice of connections is available to suit a variety of process equipment.