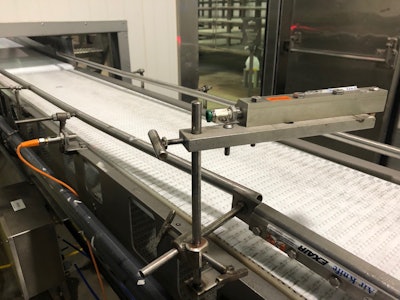
Smithfield Foods’ Kinston, N.C., facility uses air knives on two of its packaging lines to remove moisture before applying code dating, but air was discharged continuously, even if product was not coming down the line.
“Compressed air is our second-largest energy user at the facility,” states Smithfield Environmental Coordinator Charlie Prentice. “As a simple and inexpensive fix, we installed photo eyes and timers on the knives. They are now set to cut off air to the knife if an eye does not detect product within three seconds, reducing the demand on our air system and eliminating an estimated 11,351.04 kWh from our annual plant usage.”
The project was implemented in December 2020 on one packaging conveyor line where a photo-eye sensor with a timer was installed. Another packaging conveyor line had a laser with a power supply and timer installed. “Both lines were completed using parts and materials from our own stockroom,” says Prentice. “Installation was quick and easy and completed in four days.”