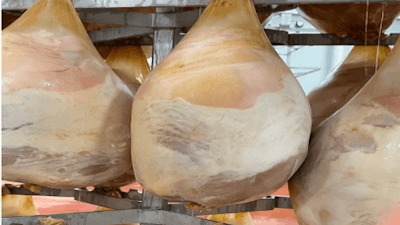
The Smithfield Foods facility in Kinston, N.C., was on a mission to decrease its cost for and waste of the continuous net used to apply smoke to hams. The netting arrives wrapped in a plastic liner inside a cardboard box.
“We saw an opportunity to increase our piece count per case by increasing the length of the netting per case,” states Smithfield Environmental Coordinator, Charlie Prentice. “Adding length was favorable to the supplier, which could decrease its packaging costs, save on shipping, and have more efficient operations.”
In turn, Smithfield benefitted from a lower cost per foot of netting and decreasing the amount of packaging waste to be hauled. The netting was increased from 1,300 ft to 2,050 ft, and the test runs were successful.
Based on the plant’s annual volume for hams, the new netting reduces the number of material cases by 2,541. “This amounts to around 2.54 tons of cardboard and plastic saved,” states Prentice. “The reduced waste helps us come closer to our goal of zero waste to landfill.”