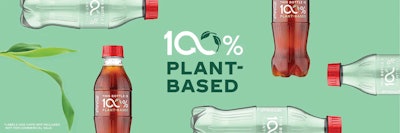
In the Packaging Technology section of ProFood World’s June 2022 issue, a report from Packaging World’s Anne Marie Mohan updated us on developments in plant-based bottles. After more than a decade of rigorous R&D work and significant investments with their respective partners, Coca-Cola and Suntory each unveiled first-of-their-kind beverage bottle prototypes made from 100% bio-based PET.
Since 2009, when The Coca-Cola Company announced the launch of the first PET bottle made partially from plants, the race has been on among beverage brands to crack the code on developing a commercially viable, 100% bio-based PET bottle with the same functionality as a petroleum-based bottle. Earlier attempts by other drinks companies to use bioplastics— specifically corn-based polylactic acid—for beverage bottles had proven disappointing, as the material lacked stability and contaminated PET recycling streams. So, when Coca-Cola’s PlantBottle, made partially from a “drop-in” bioplastic having identical properties to virgin PET, including recyclability, came on the scene, it was a game-changer.