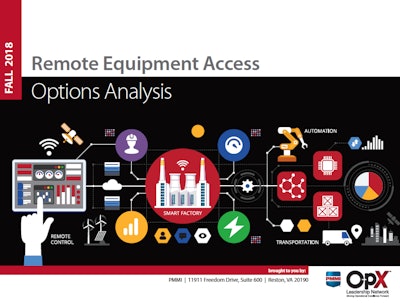
Convened by PMMI, The Association for Packaging and Processing Technologies, the OpX Leadership Network’s new Remote Equipment Access: Options Analysis guide provides a common understanding of industry methodologies for remotely accessing equipment installed in manufacturing facilities.
Based on the experience of the OpX Leadership Network’s Remote Equipment Access Solutions Group, this discussion guide was created for production teams to consider approaches for enabling access to equipment for diagnosis, potential repair and performance improvements from remote suppliers.
“Ensuring a secure remote connection at an acceptable price point is critical to securing authorization for remote equipment diagnostics for CPGs (consumer packaged goods),” says Rob Dargie, senior electrical engineer with Amway. “This was our primary objective in developing this work product.”
The technologies driving remote access are not new, but when compared to other industries, including finance and health care, adoption by CPGs is slow. The distinct and often different needs and goals of the information technology (IT) and operations technology (OT) departments cause most of the hesitancy. Despite this, remote monitoring for predictive maintenance and improved overall equipment effectiveness (OEE) is progressing, but for security reasons, the fear of data breaches and cybersecurity risks means that troubleshooting remotely continues to trail behind.
According to PMMI’s Director of Industry Services Bryan Griffen, the first thing to note is that the Remote Equipment Access: Options Analysis is a selection guide and not a tool, as opposed to many of the other OpX work product tools. “The target audience is the CPG and OEM (original equipment manufacturer) IT/OT staff, though the engineering staff is also directly implicated,” says Griffen. “The goal is to provide secure options for OEMs to remotely access the equipment they’ve developed once it’s installed in the CPG’s manufacturing facility.”
Remote equipment access can help speed machine updates, maintenance and troubleshooting. “Right now, when a machine goes down and the OEM is needed for troubleshooting, the CPG must wait until the OEM service rep can make his/her way to the factory,” says Griffen. “This could take a considerable amount of time, especially if the service rep has to fly in from another location.” By establishing a remote access link, the service rep is able to address the issue much more quickly. Automation updates and software maintenance are also greatly enhanced by the ability to remotely connect to the equipment in question, Griffen adds.
The document contains descriptions of five of the most predominant industry methodologies enabling remote equipment access, along with a comparison to the traditional, on-site options listed here:
• Direct VPN
• Converged network
• Cell modem access
• Black box
• External managed secure network
• On-site technician access
Each tactic is evaluated on seven key attributes:
•IT skills required to select, install and configure the solution, as well as provide necessary training for operations personnel.
•OT skills required to maintain, update and support operations in the ongoing utilization of the solution.
•Acquisition cost to acquire and install the hardware and software components of the solution.
•Operating cost to maintain and update the solution through staffing (internal or outsourcing), ongoing licenses and hypercare.
•Reliability of the solution based on the stability and robustness of access to the remote equipment.
•Operational protection and technical security of the factory floor (operational technology).
•Business protection to segregate the OT network from the IT network.
Additionally, the relative pros and cons of each industry approach are identified. Finally, leveraging the subject matter expertise of the OpX Leadership Network’s Remote Equipment Access Solutions Group, leadership guidance for each industry methodology is offered.
The descriptions, pros and cons, attributes, and leadership guidance provide the primary tools for analyzing and determining the best value option for a company investigating remote equipment access. Not a prescriptive document, it merely provides some significant tools for companies to use in making decisions about remote equipment access.
According to James Li, engineering manager with Abbott Labs, the Remote Equipment Access: Options Analysis guide gives CPGs a clear picture on the available technologies and connections to allow OEMs to access their installed equipment for maintenance and troubleshooting in the most economical and secure ways.
“Understanding these pros and cons allows the CPG to make an informed decision regarding the option that best fits their needs,” says Li. “At the same time, the guide provides OEMs with a finite list of connection options with which they need to be proficient in order to ensure that they are ready to make the remote connection once the CPG provides authorization.”
Remote diagnosis is not necessarily an add-on cost to the OEM, according to Griffen. “Typically, we see the CPG selecting one, or maybe two, specific methods for remotely accessing equipment. Often, the CPG has the necessary IT infrastructure already at its site. It’s simply a matter of including the correct IT hardware and software in the machine — which the CPG is paying for as part of the machine costs.”
Griffen says there will be instances where the OEM ends up paying for the implementation of the remote access, but not always. “Either way, it saves both the CPG and the OEM significant costs in downtime and service, respectively,” he states. “As long as the security is maintained, it’s a win-win.”
To download a copy of the Remote Equipment Access: Options Analysis guide, visit www.opxleadershipnetwork.org. Other helpful tools at this site include work products addressing the request for proposal process, total cost of ownership, OEE, worker safety readiness and more.