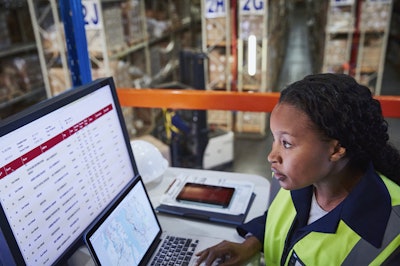
When Continental Mills deployed supply chain software from Logility across four separate divisions “that looked at the world in different ways and liked to forecast at a different level, it gained a single hierarchical structure that let each division continue to manage its business in its own way, but roll up to a comprehensive corporate view,” says Michael Burke, director of supply chain planning at Continental Mills.
Logility Voyager Solutions offers an integrated planning platform that provides the flexibility necessary to cater to business-specific challenges, says Burke. As a result, the company improved inventory turns by 20 percent, reduced inventory obsolescence from $1 million per year to almost nothing, increased resource efficiency in the forecasting process, and reduced forecast error by close to 50 percent in one division, he says.
The Logility Voyager Demand Planning system helped Continental Mills convert its businesses from an administration-heavy forecasting process to a statistical forecast, which significantly reduced time and effort. Inventory Planning and Supply Planning systems helped Continental Mills streamline the production planning process and redesign the company’s distribution network, improving capacity planning for all its manufacturing facilities.