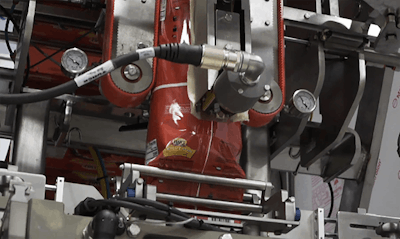
Established in 2006, Hart Food Products, Inc., Paramount, Calif, is a poultry processing company that packages retail bags of flavored chicken products, such as orange chicken, teriyaki and BBQ chicken. But recently, when issues such as bad seals, incorrect package weights, and low speeds became costly problems for Hart, they realized they needed an equipment upgrade, and quickly.
Bill Hall, president, Hart Food Products, learned of Triangle Package Machinery vertical form/fill/seal machines, a Chicago-based manufacturer of not only vf/f/s baggers, but also combination weighers, cartoners and tray loaders, through trade shows and word of mouth. [Article continues after video below].
After experiencing disappointment and various setbacks with previously purchased equipment, the poultry processor installed Triangle’s Model XM15C intermittent motion vf/f/s bagger and Model A612 Combination Weigher, along with a Markem Image printer and complete line including incline conveyor, platform and an integrated conveyor to insert sauce packets from American Mechanical, Rancho Cucamonga, Calif.
The flat bottom bag ships well and is more visually appealing than a standard pillow bag
The Model XM15C can run pillow, flat bottom and gusseted bags at speeds up to 100 bags/min. Triangle configured Hart Food Products’ system to run 2-lb. bags of chicken nuggets/prepared meals at 50 bags/min, boosting the company’s production 100% over previous rates. Their package style is a retail ready flat bottom bag, created with a multilayer laminate film. The flat bottom bag ships well and is more visually appealing than a standard pillow bag when displayed in a grocer’s frozen food section, according to the company.
Improved production, less rejects
Bagging speeds have doubled with the new system and the company is extremely pleased with the results. “Our output has improved 50-150 percent, depending on the product,” Hall says. “The dependability of the equipment and how it runs [versus our previous equipment] is night and day.”
Another benefit they’ve experienced is a dramatic reduction in rejected packages. “Rejects are down from 5 percent to less than 0.1 percent,” says Hall. He attributes the reduction in rejects to improvements in package weights and to better-sealed packages. Triangle’s X-Series vf/f/s baggers are designed with several features to help improve production, package quality, and sanitation, including servo motors on the sealing jaws and vacuum pull belts for precision motion and performance. In addition, the bagger is equipped with Allen-Bradley PanelView 10-in color touchscreen that can store up to 100 recipes and features RFID security protection specific to each operator. Using pre-established recipes, low film sensors and tool-less film spindles allow film change overs to be completed in less than a minute.
Triangle’s Model A612 Combination Weigher includes an integrated infeed system and Allen-Bradley Control-Logix PLC to calculate the best weight combination of the 12 holding chambers to achieve highly accurate target weights. Hart’s scale features 6-in x 6-in buckets and a tilted, motorized infeed that can be adjusted from 0-deg to 15-deg incline. This helps the company fill a full range of today’s products, including larger and sticky products such as cooked rice. Equally important, the company is now in a better position to add new products, such as meal kits, that the previous equipment couldn’t package. With these limits removed, they are now able to package blended products such as chicken and vegetables or chicken and rice, along with a sauce pouch.
Improved sanitation
The company also appreciates the fact that the equipment is easy to clean and designed for a washdown environment. Triangle’s X-Series bagging machines are available in four levels of sanitation, including painted frames, stainless steel frames, stainless steel washdown, and 3-A/USDA-certified models. Meat and poultry customers appreciate the bagger’s clean design features such as pitched top plates, fully welded stainless-steel frame, and cross members that are rotated 45 deg, all of which facilitate better and faster cleaning. In addition, a pivoting control box provides four sides of machine access.
Film infeed on Triangle’s Model XM15C intermittent motion vf/f/s bagger
Hart Food Products took advantage service and support from Triangle, as well. A team from Hart traveled to Triangle’s Chicago headquarters for training and machine check-out, followed by additional training at Hart’s plant in California. “Our staff went to Triangle for training, then a tech came out here for a week to install it and provide additional training,” says Hall. “They were extremely professional, and we are very satisfied.”
Lessons learned
The fact that Triangle’s packaging equipment is manufactured and supported in the U.S. was a welcome change for Hart Food Products. After experiencing various challenges with their previous system, the company is thoroughly enjoying the benefits provided by their Triangle system. “The biggest financial mistake ever made at Hart was three years ago when we purchased a bagger and scale because it cost less than half that of domestic equipment. It was a disaster and was removed after one year. The monthly cost of the loan for the Triangle pack line is less than the monthly overtime and product rejection costs. My mistake was looking at gross cost and not monthly payment and operational cost savings,” admits Hall. “We’ve bought machines from overseas sources and the contrast of the two is startling. We have manuals now that are in coherent syntax, not poorly translated. Previously, if we even got a manual, it was poorly translated and virtually useless. Tech support was as minimalist as possible, and they never got it right.”
What advice would he give to other companies looking for a new bagging or weighing system? “You can’t apply a cookie cutter solution to people’s packaging needs. It’s not going to work the way you need it to, and you’ll have a lot of problems. I don’t care who you buy but look at monthly payments versus overall price. Compare that to savings on overtime, rejects, and downtime. We come in every morning and know our system is going to power right up.”