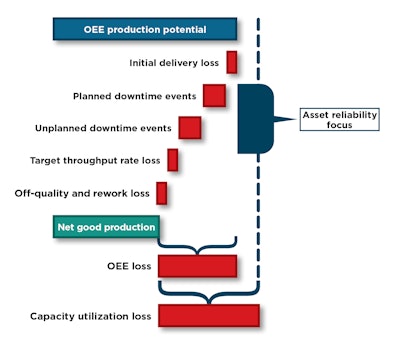
Daniel Lorusso system sales director, BW Packaging Systems
Dan Sileo co-founder, partner, and chief manufacturing coach, FSO Institute
Stephen M. Perry, PH.D. co-founder and coach, FSO Institute
While there may be as many definitions of asset reliability as there are consumer packaged goods (CPG) manufacturers to define it, most all agree that the primary goal of undertaking an asset reliability initiative is zero downtime and maximizing asset life.
PMMI’s OpX Leadership Network recently commissioned the Asset Reliability Solutions Group to undertake a work product on asset reliability in order to get CPGs and original equipment manufacturers (OEM) on the same page regarding definitions, key performance indicators (KPI), calculations, and leadership guidance when developing an asset reliability initiative. The work product is nearing completion and will be available later this year.
See it on PACK EXPO Connects' website through March 2021: Vertical Conveyors for pallets, by QIMAROX VERTICAL CONVEYORS. Preview the Showroom Here.
The team discovered early on that perhaps one of the best ways to understand asset reliability is in its relationship to overall equipment effectiveness (OEE). As shown in the graphic below, asset reliability initiatives are focused on two key areas within OEE loss: planned downtime events and unplanned downtime events. These are the very events that inhibit a machine from performing its intended function or from doing what it is supposed to do, when it is supposed to do it.
In this soon-to-be-released OpX work product, the focus of an asset reliability initiative to address these events is based on three categories of KPIs:
1. People KPIs–Focused on labor factors, including total production maintenance labor costs, actual fully loaded operations labor costs, overtime maintenance costs and hours, contractor costs and hours, planned and unplanned maintenance costs, preventive maintenance costs and hours, and others.
2. Operating KPIs–Focused on operating factors, including plantwide average downtime (planned and unplanned), plantwide scheduled production hours, total plant MRO (maintenance repair operations) budget to spend, OEE, availability, uptime, stores inventory turns, mean time between failures, mean time to repair or replace, and others.
3. Financial KPIs–Focused on financial factors, including stocked MRO material inventory value, ratio of replacement asset value (RAV) to craft wage headcount, total maintenance cost as a percent of RAV, opportunity cost due to unplanned downtime, and others.
For each KPI, there is a corresponding definition, leadership guidance, and calculation (where needed) to get CPGs and OEMs speaking the same language when it comes to asset reliability. In addition, the KPIs are categorized by stage in the asset reliability journey, e.g. which KPIs are necessary at the beginner stage as well as those needed at later stages.
For CPGs trying to determine the value of an asset reliability initiative—the “size of the prize”—the Asset Reliability Value Calculator can help determine the potential value of missed opportunities that could be gained by improving line reliability. The focus here is on improving the reliability of the critical asset or the main bottleneck on the line in addition to the processes involved in the entire manufacturing process.
Collaboration can yield significant improvements in OEE by focusing on opportunities to reduce the impact of planned and unplanned downtime and, instead, drive to zero downtime.
An important factor in understanding asset reliability is in its relationship to overall equipment effectiveness (OEE). Asset reliability initiatives are focused on two key areas within OEE loss: planned downtime events and unplanned downtime events. Source: PMMI’s OpX Leadership Network OEE guidelines report.
Other articles you may be interested in:
Major Trends in Modern Health Today
Security, Remote Access, and Manufacturing Data
Coffee Pod Co-Packer Realizes Perks of ERP System
Case in Point: Green Thumb Industries and BW Packaging Systems
As a prelude to the next OpX Asset Reliability document release, FSO Institute checks in with two members of the OpX Asset Reliability Solutions Group—Chris Darling of Green Thumb Industries (GTI) and Daniel LoRusso of BW Packaging Systems—to weigh in on some of the greatest asset reliability challenges and how the OpX guidance document could help solve some of those challenges. Dan Sileo, chief manufacturing coach with the FSO Institute, weighs in as well.
FSO Institute: Chris, you were there from the beginning in developing the OpX Asset Reliability document and clearly saw the need for it. What are some of the challenges GTI faces regarding asset reliability?
Darling: The priority for GTI was to start building an asset management system and reliability strategy. The solutions group was an opportunity to help develop and educate everyone on the value and need. We are in a business that is maturing, as well as we are in an emerging high-growth phase. Therefore, these processes will help to ensure our future success. Helping to develop the OpX asset reliability document was a great way for us to share, learn, explore, and understand the challenges that are impacting other consumer packaged goods companies today in building out the reliability initiatives will pay huge dividends in the future, as our systems will be reliable and allow us to fulfill our safety, quality, delivery, and cost objectives.
FSO Institute: Dan, as Chris noted, GTI is in the early stages of developing their asset reliability initiative. In your experience with both emerging and mature consumer packaged goods (CPG) companies, what are the most significant challenges you’ve seen in asset reliability?
Sileo: One of the biggest challenges I’ve seen time and time again is getting everyone on the same page regarding the value of assets. For example, the shop floor operators and frontline leadership have a strong desire to deliver results and product to the customer, but may not understand the long-term benefit of investing in the assets. As such, there is a tendency to shortcut, delay, or skip scheduled maintenance programs like autonomous maintenance or preventive to deliver the immediate need. Most manufacturers know that this can create a vicious downward spiral in OEE (overall equipment effectiveness). As leaders, we have an obligation to invest in these associates to explain the “why” and demonstrate the “how” of increasing asset reliability by investing in the equipment, but are too often consumed in other priorities and don’t act on this as a priority.
FSO Institute: Chris, what solutions have you put in play, and how might this OpX asset reliability guidance document help with those and other solutions you’re considering?
Darling: We are still very early in our journey. We are building teams with a proactive focus in mind, educating on the value of reliability and the processes. We are starting from the ground up, collecting data focused on our most critical assets and then implementing our CMMS (computerized maintenance management system) solution for work management and materials management to drive some of the baseline KPIs highlighted in the solutions group document. Once we have established our baseline objectives, we will start building more advanced processes and KPIs.
FSO Institute: Dan, of the challenges you highlight above, what are some of the solutions you’ve put in play to improve the reliability of assets in the drive to zero downtime?
Sileo: In one company I worked with, we trained on the importance of planned maintenance, but then made it important by putting a process in place that if scheduled PM (preventive maintenance) time was moved, it needed plant manager approval, and if by more than 24 hours, they had to get VP approval. This put pressure in the system to hold to the scheduled maintenance, and we were then able to show a greater than 4% improvement in OEE (almost an hour a day).
FSO Institute: Daniel, you also became a contributor in developing the OpX asset reliability document and clearly saw the need for it. From an OEM perspective, what challenges have you faced regarding asset reliability, especially in working with your CPG customer base?
LoRusso: As an OEM, we define value to our customers in a variety of ways. It’s easy to see the value of our innovation investments because machines with new technology, more intuitive operator interfaces, and quick and easy product changeovers are often well publicized as marquee improvements. However, our investment and efforts to make our machines more reliable and robust may go unnoticed by potential customers because of how difficult it is to quantify reliability back to an operation’s bottom line.
Each year, BW Integrated Systems, a BW Packaging Systems company, makes significant investments in product development. I’m excited to see the development of tools that can help our customers better quantify the value of a reliable machine. I have seen too many instances where we’ve been asked to replace or modify a machine that had a cheaper price tag at the time of original purchase, but ultimately hindered our customer’s entire packaging operation. For years, our customers have been looking for a way to “see into the future of a machine,” and I’m glad they now have a tool to do just that. Hopefully, a better understanding of asset reliability paired with the [OpX] total cost of ownership tool will help guide our potential customers toward machine centers that will foundationally improve their business.
FSO Institute: What solutions have you put in play and how have they been incorporated into product development at BW Packaging?
LoRusso: As I stated before, BW Integrated Systems has a strong and purposeful innovation plan. We invest year after year to keep our marquee products at the top of their game, and we also develop new solutions that help our client’s meet their ever-changing packaging needs. In each case, sitting with our customers and documenting their needs, likes, and frustrations are always the first steps.
We interviewed dozens of clients in multiple countries who have experience with our machines, as well as our competitors. This gave us a broad understanding of what was needed. In each case, machine reliability was a key factor, but it was a factor that was difficult to quantify.
One example of finding reliability through a reduction of planned downtime is a move away from compressed air and pneumatics. In our most complicated machines, we have dozens of valves and cylinders, all of which need frequent maintenance through planned downtime. By replacing these components with systems that require less maintenance, we have increased the potential uptime and put real money back in our customers’ pockets.
We all understand that a machine with better uptime and limited planned/unplanned downtime is the preferred machine. Yet even as an equipment supplier, it is hard for us to financially compare what additional uptime could do to a customer’s bottom line. The example of the Asset Reliability Value Calculator is such a good tool to show the benefits of a machine or upgrade package that correlates to less downtime and more production.
About the Case in Point Series
In the past few years, PMMI’s OpX Leadership Network has produced more than 20 manufacturing process-improvement documents for CPGs and OEMs. The FSO Institute has facilitated the adoption and implementation of these documents, especially for food and beverage manufacturers. In this Case in Point series with the FSO Institute, ProFood World presents actual cases to show just how CPGs are using OpX documents to improve their overall manufacturing health and their collaboration with OEMs and other suppliers. Learn more at www.opxleadershipnetwork.org and www.fsoinstitute.com.