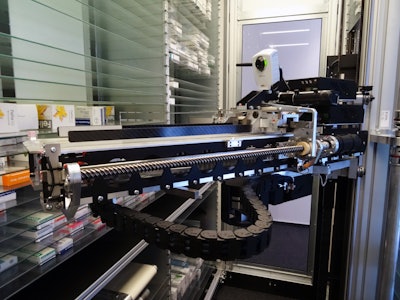
BD Rowa has introduced a pouch packaging center designed as a cost-efficient device for the packaging of solid, oral medicines. The unit, called the Rowa Dosa system, is suitable for unit, multi- and combination doses.
The Rowa Dosa system packages solid oral medicines in patient-specific blister pouches. The system can be expanded with modular components and offers medication safety, packaging up to 700 medicines for patients.
Rowa Systems from Becton Dickinson systems and accessories automate medication storage and dispensing in hospital pharmacies. The pouch packaging center uses bearing technology from igus, the Germany-based manufacturer of motion plastics.
The automated system can put together the desired combination of medicines in up to 700 canisters, and package the combination in a blister pouch. The economically sized system, which can have a width as little as 3.08 meters and a depth of 1.14 meters, also prints the patient’s name, content and when the medicine needs to be taken on the pouch.
The long side of the machine includes canisters from which the medicines are individually dispensed. On the inside is a series of moving downpipes. The bottom end includes collector funnels mounted on a carousel-like circulation system. The patient-specific medicine ratios are collected in the funnels and then blister-packaged.
The rapidly moving circulation system needed a high degree of availability. Rowa design engineers required a long service life, since the machine must operate 24/7, as well as a low degree of abrasion, since the downpipes that transport medication are not separately packaged.
For the same reason, BD Rowa requested a lubrication-free linear and curve guidance system. Additionally, criteria included the ability to move through a small curve radii and as little friction as possible in order to decrease the amount of drive energy needed, minimize vibrations and keep noise levels at a minimum.
For horizontal guidance for the downpipes, drylin W profile guides made of hard-anodized aluminum are used. The guides have extra height and width to absorb greater tilting forces and ensure stable guidance of the downpipe.
Engineering teams devised a customized solution for the narrow sides of the circulating system. They designed 180-degree curves with a radius of 80 millimeters. Sliding through tight curves also necessitated plastic sliders that maintain stability during movement into the tight curve, even at high speeds.
The customized unit made it possible to include another special function. On the narrow sides, the guides can be opened in order to replace the individual bearings. The bearings pass over this section every time the unit is used. Several hundred guide elements of the type drylin W 10 liners, which are made with high-performance, maintenance-free iglide J material, are built into each Rowa Dose system.
The combination of materials ensures maintenance-free and wear-free operation of the circulating system over a long period of time. Tests performed with the first prototypes by Rowa confirmed the system’s durability and smooth operation.
Becton Dickinson engineers have been frequent users of igus products. Rowa, which became known in 1996 with automated picking and packaging systems for chemist shops and pharmacies, has systems that are used in more than 40 countries worldwide.
The core of the Rowa Vmax machines is the patented “picking head,” a gripping system that moves between the two storage rows and can move into both rows. A drylin high felix thread from igus with plastic nuts ensures precise linear movement into the shelf.
The ratio of diameter (14 millimeters) to inclination (25) creates the basis for fast medicine “picking” processes. The patented geometry, compared to conventional spindle systems, enables a higher degree of efficiency as well as a service life two to three times as long.
igus also supplies the high helix drives for the Rowa Vmax systems as a ready-to-install system with a plastic nut and ball bearings, and every single drive is tested in the factory. The testing is necessary because of BD Rowa’s requirements regarding the precision and positioning accuracy of the drive components.
Energy chains from igus are also used in Rowa automatic order picking machines. Short working cycles and tight bend radii on both sides are required for this application. The chains come pre-harnessed and ready-to-install and have undergone extensive testing in igus’ test labs.