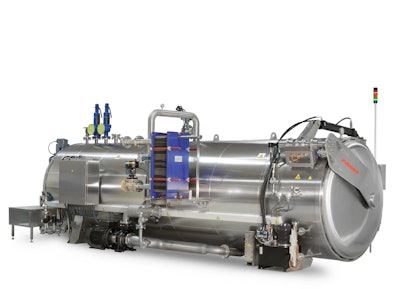
This content was written and submitted by the supplier. It has only been modified to comply with this publication’s space and style.
Surdry rotary retorts turn cans, jars, pouches, and other containers during sterilization and cooling processes. The purpose is to move food content around while cooking to accelerate the heat transfer inside the container and allow certain types of food to cook evenly. This process helps prevent unwanted side effects such as discoloring or burning of the food product.
The rotary retorts feature a robust design for clamping baskets or stacks of trays individually to ensure the loads are well supported, minimizing damage to the containers, baskets, and trays. The clamping mechanisms, as well as alternate moving parts like the rotor shaft or supporting rollers (trunnions), are designed for heavy-duty movements and a lengthy lifespan.
Rigid packages, such as cans, jars and bottles, are loaded in baskets with perforated divider pads set between the layers of packaging, allowing for maximum utilization of the retort basket. The divider pads are perforated sheets made of plastic material. The number of layers and packages per layer depend on both the size of the package and the retort.
The rotary retorts can additionally operate in an oscillating mode to accommodate products that do not require full rotation. This process helps pouches and similar-shaped, less-rigid containers reduce the cost of complex trays needed for full rotation. The retorts are available in vessel diameters between 1,400 and 1,700 mm, and feature a maximum five-basket capacity.