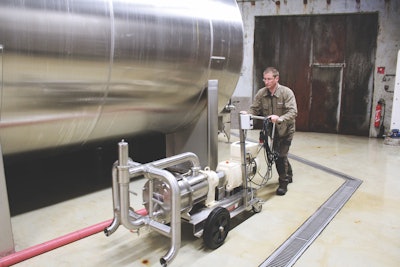
Don’t underestimate the importance of pumps. Transferring food or beverage products from one area to another in a facility, pumps serve as the infrastructure for the manufacturing process. They play a crucial role in keeping production moving along efficiently by minimizing downtime, lowering lifecycle costs and maximizing productivity. That’s why food and beverage manufacturers carefully consider a variety of factors when selecting pump technology, including versatility, durability and reliability, sanitary design that simplifies cleaning, energy efficiency, and ease of maintenance.
“If you imagine a process room, the pump is at the heart of it — just like the heart of the body,” says Bob Garner, engineering manager for Glendale, Wisconsin-based Ampco Pumps Company. “It’s the pump that basically delivers the beverage or food throughout the process room. Whether it’s through heat exchangers or filters or dispensing systems, the center of the process room is the pump. So if a pump goes down, the rest of the plant or room goes down.”
Of pump and circumstance
Application and rightsizing are some of the most important considerations in determining the appropriate pumping system for a facility, keeping in mind viscosity of the product, shear sensitivity, and pressure and flow rate. Centrifugal pumps and positive displacement pumps are the most common pump technologies in the food and beverage manufacturing industry.
A centrifugal pump is often used to transfer water, oils and other low-viscosity products. The pump’s rotating impeller generates suction and uses that centrifugal force to thrust the fluid against the outer wall and force it out of the pump’s discharge port. A centrifugal pump not only allows operators to pump large quantities of fluid at a high flow rate, but they can also adjust the flow rate, making a centrifugal pump a versatile and energy-efficient option.
Manufacturers that produce viscous foods typically use positive displacement pumps, such as rotary lobe pumps, progressive cavity pumps or diaphragm pumps. They all operate on the same principle: The cavity on the suction side of the pump expands, lowering the pressure and pulling in the product. The product is then carried around the lobes to the discharge side, where the cavity contracts, generating pressure. The difference in pressure pushes and pulls the product simultaneously, exerting force to create flow with no or low shear. That means it can maintain product integrity with gentle product handling. However, unlike a centrifugal pump, a positive displacement pump will produce the same flow rate independent of discharge pressure.
Hygienic standards
Sanitary design is also an essential feature of any pumping system. Manufacturers should invest in pumps that meet standards set by 3-A Sanitary Standards, Inc., a nonprofit that advances cutting-edge hygienic equipment design and technology for the food, beverage and pharmaceutical industries. Pumps should also offer clean-in-place (CIP) capabilities that allow an operator to run a cleaning agent through the pumps to prevent contamination and bacterial growth. In addition, pumps should not have cast surfaces, crevices or nooks, which allow bacteria to harbor as well as inhibit drainability.
“Make sure that it can be fully cleaned,” says Michael Druga, president and CEO of Raleigh, North Carolina-based SinnovaTek, which develops and sells thermal processing equipment and pumps. “Meaning not just that you can run your caustic through it, but that any material or residue inside the body of the pump can get flushed out during the CIP cycle, making sure it can drain. You always want to make sure you can fully drain out the body of the pump.”
Anatomy of a robust pump
Durability is another key component of efficient pumps. To ensure reliability and lower lifecycle costs, Garner recommends that manufacturers purchase pumps made from the most robust materials they can afford. “You want to use the strongest materials available,” he says. “You want to make sure that all the components, bearings and gears are durable for the life of the pump.”
For example, while most food and beverage pumps are made from standard 316 stainless steel for corrosion resistance, Garner suggests purchasing some pump components consisting of heat-treated stainless steel or 17-4 PH stainless steel, which is more than twice as strong as 316 stainless steel. They can handle abrasive products, high temperatures and high pressure better than thinner materials, helping to prevent damage like shaft breakage and component contact from piping misalignment.
The architecture of pumps should also be designed for strength and to diminish internal wear. Tight internal clearances are one of the most important factors that affect pump performance and total cost of ownership. “The clearance, or the distance between where the parts come into contact with the other parts, has to be tight. Otherwise you lose pressure and efficiency,” Garner says. “[It also affects the food product] because food could shear back through those loose clearances and damage the product.”
“You want tight clearance whenever you have a high-pressure application,” says Bob Wells, OEM sales manager for Middleton, Wisconsin-based Fristam Pumps. “You don’t want those shafts deflecting and rubbing internally inside the pump to wear it out.”
To further avoid shaft deflection, pumps should have balanced rotors and oversized bearings as well as short shafts with large diameters. “Shaft design, rotor design, bearings — those things lead to more durable pumps when they are rightsized for the application,” says Zach Suardini, application engineer for Fristam. “They help extend the life of the pumps and prevent premature failures and unplanned maintenance.”
Seals are also crucial for durability as well as for maintenance efficiency. Manufacturers need to select the seal material appropriate for their pumps because the seal is the wear part that they will need to routinely replace due to fatigue. When pumping water or other less viscous or abrasive products, cost-effective single seals will typically do the job. But when manufacturers use their pumps for abrasive or sticky products that require more pressure and heat, heavy duty seals come into play. For example, Fristam offers double mechanicals seals with hard seal face coatings, such as silicon carbide and chrome oxide. They keep the seals cool, preventing abrasive products from getting stuck in the seals and ensure the seals remain clean. “Typically, the main cause of seal failure is heat, so anything you can do to keep it cool and anything you can do to keep it clean will only help extend the seal life,” Suardini says.
Manufacturers are also looking for ease in replacing the seals. Fristam and Ampco are responding to those demands by offering front-loading seals. Those seals allow production personnel to service the pump and replace the seal without having to take the pump body apart or use special tools. It not only eases maintenance but also reduces downtime and requires fewer maintenance parts to stock. “That means you can change the seal without having to remove the piping and the pump body, which sometimes these bodies are so big you would usually need a crane to get them off,” Garner says. “But with a front-loading seal, you can remove and replace the seal without taking the whole pump apart.”
To reduce downtime during maintenance, Grundfos, a manufacturer of pumps based in Denmark, recommends having a duty standby pump. Should an active pump fail or go down for unplanned maintenance during processing, a manufacturer can use the standby pump while the active pump is repaired. More suppliers like Grundfos are implementing duty standby pumps so that they automatically go into effect when the active pump fails. “This duty standby feature is built into the controller of our variable frequency drive (VFD). The two pumps can talk back and forth through the frequency drive controllers, and one pump can operate the other pump,” says Mike Kelzer, product manager at Grundfos. “If one pump goes down, it knows to turn the other pump on if there was a failure with it. It’s built into the variable frequency drive, and it’s in the control of the variable frequency drive that we’re able to do this rather than having controls on the wall.”
Efficiency at the pump
Manufacturers are also seeking to achieve energy efficiency from their pumps today. It is now common to see pumps operated by motors controlled by VFDs. VFDs control motor speed by varying the frequency of the power sent to the motor, achieving significant energy savings. “The variable frequency drive costs have come down a lot in the last 20 years, so people are using them a lot more to dial in their speeds,” Garner says.
But Grundfos is taking the VFD concept to the next level with its stepper motor technology, which uses a microcontroller to deliver precision and control to its dosing pumps. “Our stepper motor technology can very precisely turn a pump or rotate it using some complex algorithms to tell the motor to spin at certain times, so when and where to position the motor and at what time they should do it,” says Jared Gabel, product manager at Grundfos. “So what’s going on now, is that the pump is actually able to run a full diagnostics check of the system around it. For a metering pump or a positive displacement pump that has a suction and discharge stroke, the pump knows now when it’s going into a suction or a discharge stroke and how fast it should spin based on a feed rate that the customer or end user needs. That all translates into high precision and accuracy. And when we look at the lifecycle cost, we can see a very quick payoff.”
Pumps can attain energy savings via mechanical and hydraulic means as well, according to Gabel. For example, he says Grundfos can optimize the efficiency of its centrifugal pumps by simply changing the curvature of the blade inside the impeller. The company also gains efficiency with its centrifugal pumps by eliminating eddies and turbulence, which results in better flow patterns that reduce pressure loss.
Double duty
While food and beverage customers are demanding energy savings as well as durability and sanitary design from their pumps, they are also looking for pumps that are versatile enough to handle more than one task. One of the most popular pumps on the market today is the twin screw pump. More manufacturers are using this pump because it combines the best aspects of a positive displacement pump and centrifugal pump into a single pump.
A twin screw pump features twin rotating screws that provide a gentle pumping action. As the pump rotates, the two screws intermesh to form closed chambers that are moving in an axial direction. The chambers fill with the pumped product, moving it from the inlet suction side of the pump to the higher pressure discharge side of the pump. The movement of the chambers creates low pulsation or pulse-free flow for gentle product handling and high suction. The axial balancing eliminates metal-to-metal contact of the parts, extending the life of the pump.
Unlike a lobe-style positive displacement pump, a major advantage of using a twin screw pump is that it can efficiently transfer both liquid and viscous products — including products with entrained air — at variable flow rates, pressures and temperatures. With the ability to substantially increase the flow rate, the twin screw pump is also able to conduct CIP without attaching a separate centrifugal pump to it. “You’re able to turn up the rate of these pumps so that the same pump can act as both the product pump as well as a CIP pump,” Druga says.
Druga has seen firsthand how a twin screw pump can increase efficiency and productivity for a food manufacturer. Last year a chocolate company based in the southwestern region of the United States installed a QTS Twin Screw Pump from SinnovaTek. The twin screw pump replaced an energy-intensive helical screw pump system that had difficulty consistently maintaining the heated temperature of the chocolate. In addition, the company had to clean and maintain the helical screw pumps every six weeks because of the buildup of chocolate, a particularly abrasive product for pumps due to the crystallized sugar in it. With the QTS Twin Screw Pump in place at the chocolate factory, the company is able to process its chocolate at a faster flow rate and has not had any maintenance issues to date.
“They went from basically 22 gal a minute up to 30 gal a minute,” Druga says. “So they saw a pretty significant improvement just because they weren’t losing temperature and being able to maintain that continuous flow without having to stop.”
Another popular pump in the food and beverage industry is the eccentric disc pump, which optimizes the production process with gentle product handling, hygienic design and significant product recovery. An eccentric disc pump features a disc that is placed inside a pump cylinder. The cylinder and pumping element are mounted on an eccentric shaft. As the eccentric shaft rotates, the pumping element forms chambers within the cylinder, which increase in size at the intake port, drawing fluid into the pumping chamber. The fluid is transported to the discharge port where the pumping chamber size is decreased. This action squeezes the product into the discharge piping.
Yonne, France-based Bailly LaPierre uses the SLS Series Eccentric Disc Pump from Mouvex to make its Cremant de Bourgogne, white and rosé sparkling wines. The company says the pumps are crucial to producing its 4 million to 5 million bottles of wine a year. The pumps deliver a low shear rate for gentle product handling, volumetric consistency, no slip, and a strong vacuum and compression effect for enhanced line stripping and optimized product recovery. In addition, the SLS Series Eccentric Disc Pump features a seal-less design that incorporates a hermetic pump head with a self-adjustable eccentric shaft protected by a double-wall stainless-steel bellow that ensures long life and product safety.
“Mouvex pumps have many benefits for us,” says Mathieu Cerveau, cellarman at Bally LaPierre. “The high flow rates are a key feature. Since we deal with big volumes of liquid, we need a big flow. Another great feature is the strong suction. Because the pump is located in the pressing area, it has to suck the liquid from a lower level and send it through about 40 meters of piping. This isn’t possible with some other pumps. Additionally, just as we have designed our presses to handle the grapes as gently as possible, we love the fact that Mouvex pumps feature no excessive shear that puts friction on the wine. But the best benefit for us is the higher rate of product recovery. The Mouvex pump can completely drain all of the juice from the piping and from inside the tanks.”
A key to the Mouvex pump’s enhanced product-recovery capability is its unique conveying principle. The eccentric shaft drives the stainless-steel static cylinder and the moving piston, generating a circular movement. Through this movement, the inner and outer chambers are formed, which displace the liquid from the suction side to the discharge side with consistent and accurate flow. Given that the pump can run dry, the rotation of the parts creates a compressor effect that facilitates the stripping of the discharge lines.
“The Mouvex pump is the most efficient solution to totally draining our piping, not only for our pressing operation but for transferring and bottling as well,” Cerveau says. “The pump can easily push all of the wine out of a tank and into our bottling workshop.”
While pumps may not necessarily stand out on the plant floor compared to other equipment, they are essential to the productivity and efficiency of the manufacturing process. “[Pumps are] the quiet component of a plant because it is a small price compared to all the larger components,” Druga says. “But the quality of your systems relates directly to the quality of your pump, both from an efficiency standpoint as well as the consistency of pumping.”