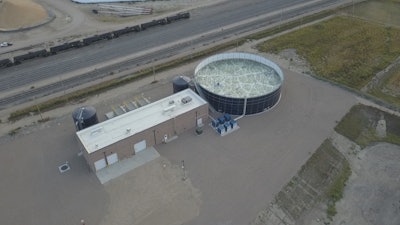
Garden City, Kansas’ wastewater treatment facility did not have the capacity to handle the projected biological load generated by a large milk processing plant. In fact, the municipality was already facing increased demand for quality water for agricultural and industrial use. Dairy Farmers of America (DFA) agreed to build a 2.5-million-gal, use-specific wastewater treatment plant using membrane bioactivity and UV disinfection that would successfully combine the plant’s properly treated effluent discharge with the city’s effluent at a shared outfall storage system. This arrangement allows Garden City to provide the combined effluent for the area’s much-needed agricultural irrigation.
Reducing the dependence on the water supply from the municipal water system by continuously capturing available reusable water produced from the 24/7 operation at DFA was of paramount importance, says Alan Low, Shambaugh & Son’s senior vice president and project manager. “Process water push valve arrangements were designed for the entire liquid process portion of the plant. This allows every product transfer, to and from silos, to and from process systems, and to and from intermediate work in progress, to be captured for reintroduction into the process system,” states Low.
When evaporators are brought online and taken offline, it causes initial product concentrate that is low in solids and results in unsellable product that not only wastes energy to produce, but is typically sent to landfills. “To address this waste issue, product recovery tanks were designed to store the lower solids produced by the evaporators during startup, when building solids and during shutdown as water is pushed through the evaporator to clear product from the evaporator,” Low says. Recovery tanks were sized to handle the volumes produced during these times and allow for the re-blending of the product back into the evaporation process.