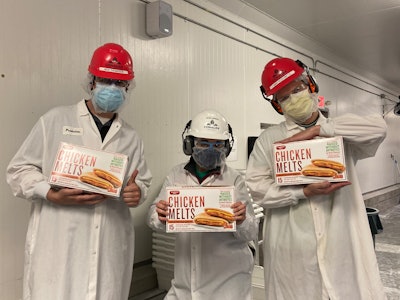
In September 2019, Conagra Brands’ Milwaukee team initiated a program to limit cheese yield loss. Initially, identifying and justifying the project capital was difficult. Gathering, separating, and weighing cheese waste throughout various production processes appeared to be a daunting task.
But through an intense process investigation, many loss points were identified and corrected. The team discovered that a large contributor to food waste was cheese miss-cuts, and it rectified the problem through editing standards, optimizing run settings, and conducting preventive maintenance on machinery. This program resulted in approximately $530,000 in annualized savings and the avoidance of 130 tons of edible cheese waste per year. Also as a result of the program, the facility was able to increase production with the same amount of incoming ingredients.
See it Live at PACK EXPO Connects Nov. 9-13: Increase Line Performance with Packer for Bulk, Variety, Display and Single Flavor Packing, by BluePrint Automation (BPA). Preview the Showroom Here.
“In the three months prior to the program implementation, the site would have produced close to 1,900 tons of solid waste,” says Tracy Kayhanfar, senior director, environment. “Through continued efforts, the plant is now saving 130 tons of or almost 7% of total waste produced by the facility per year. With an initial investment cost of $111,545, the solution yielded annual savings of $537,055, with a [return on investment] of less than a year.”